The rare earth elements (REEs) are used in a wide range of applications, including clean energy technologies. Their unique properties make them indispensable in applications such as permanent magnets and catalysts and as polishing agents. Rare earth permanent magnets constitute the leading end-use market, with a global demand share in 2020 of 29 per cent (Figure 1).
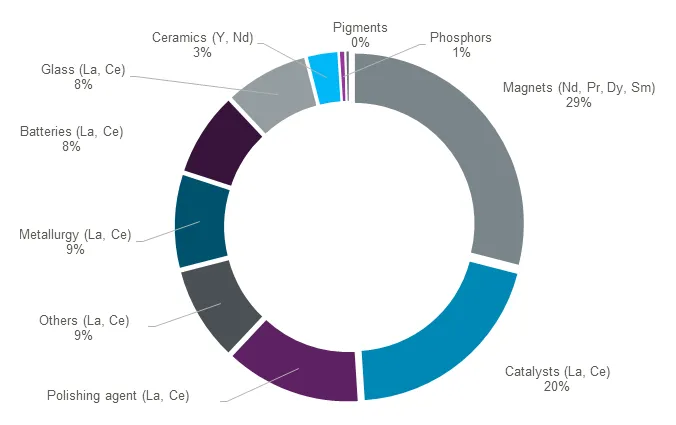
REEs are subdivided into two groups, based on their chemical properties (Tables 1 and 2). Scandium (Sc) is sometimes classed as a REE; however, it has different properties that set it apart from this group.
The key elements for the manufacture of permanent magnets are neodymium (Nd), dysprosium (Dy), praseodymium (Pr) and terbium (Tb), used in Nd(±Dy±Tb±Pr)-iron-boron magnets, and samarium (Sm), which is used in Sm-cobalt magnets.
It is important to note that deposits of individual REEs don't occur in nature; however, some deposit types can be more light (LREE) or heavy (HREE) enriched.
Element | Element symbol |
---|---|
Lanthanum | La |
Cerium | Ce |
Praseodymium | Pr |
Neodymium | Nd |
Promethium | Pm |
Samarium | Sm |
Europium | Eu |
Gadolinium | Gd |
Element | Element symbol |
---|---|
Terbium | Tb |
Dysprosium | Dy |
Holmium | Ho |
Erbium | Er |
Thulium | Tm |
Ytterbium | Yb |
Lutetium | Lu |
Yttrium | Y |
Acquiring rare earth elements
Supply chain
The REE supply chain is complex and global, and includes multiple actors that interconnect to deliver the materials, components and REE-bearing products that are essential for a range of applications. The supply chain comprises the stages of exploration, extraction, processing, manufacture, use and end-of life. Each one of the stages includes material transformation processes, in which REEs are transformed into different forms (for example, from ores to oxides and metals).
REEs are fundamental for decarbonisation technologies, such as wind-powered energy generation (wind turbines) and electric vehicles, which rely on the availability of permanent magnets. REE availability is highly concentrated in China and the overall market has been volatile, with rising concerns around security of supply in the global and UK communities.
The outlook for REEs is one of increasing demand for all markets, but especially so for permanent magnets and metal alloys and the related REEs (Nd; Dy; Pr; Tb). There are several challenges to bringing new supplies on stream that extend beyond the physical imbalance between supply and demand. Environmental, economic, social and political challenges also exert significant influence on the future of the REE supply chain.
In Met4Tech, we attempt to understand and quantify the UK REE supply chain, including the reverse options focusing on wind turbines and electric vehicles as key applications. Our aim is not only to identify global influences and bottlenecks that may affect the UK, but also, and more importantly, the identification of circular economy opportunities.
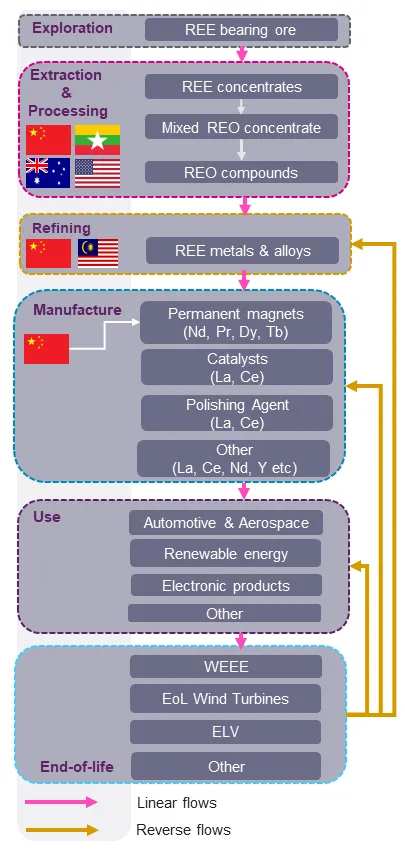
Exploration
Exploration for REEs experienced a boom that started in 2010, after China placed export restrictions on its supply of REEs to the rest of the world. This boom has developed over the past decade, further fuelled by increased prices and increased demand for certain REEs.
Exploration for REEs occurs on every continent on Earth, with the exception of Antarctica. Some of the projects and target areas are at the very early stages of exploration, whilst others are more progressed and have published resource and reserve estimates.
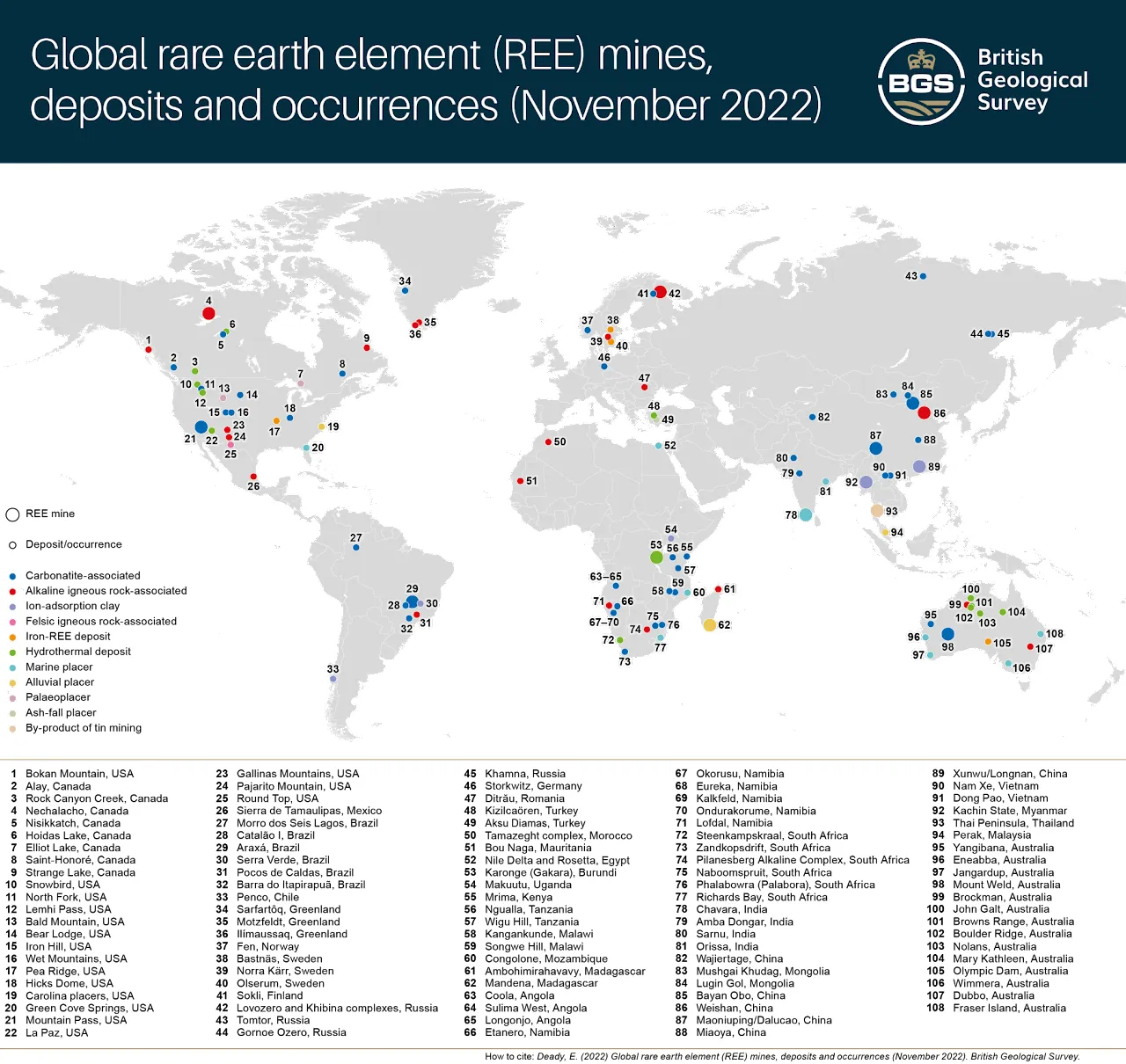
Deposits, occurrences and mines that contain REE occur in a range of deposit types and in a variety of geological settings. The most important deposits are associated with carbonatites, ion adsorption clays and alkaline igneous rocks.
- Carbonatites are igneous rocks that contain more than 50 per cent modal carbonate and are typically enriched in LREEs
- Ion adsorption clays typically occur as tropical weathering crusts on top of igneous lithologies such as alkaline granites. During weathering, the REEs are released from primary igneous minerals and are then adsorbed or bonded to secondary clays, creating an easily processed, REE-rich deposit. The REE content of ion adsorption clay deposits can be variable but currently most of the world's HREEs are extracted from these deposit types
- Alkaline igneous rocks can be important hosts for REE mineralisation; for example, REEs are extracted from a large igneous complex in northern Russia. Other deposits associated with igneous rocks that contain the mineral eudialyte could be a potential future source of REEs if appropriate processing technologies are developed
REEs are also sourced from mineral sands and placers across the globe. Monazite and xenotime are the main minerals produced from these particular deposit types
Reserves of contained rare earth oxides (REOs)
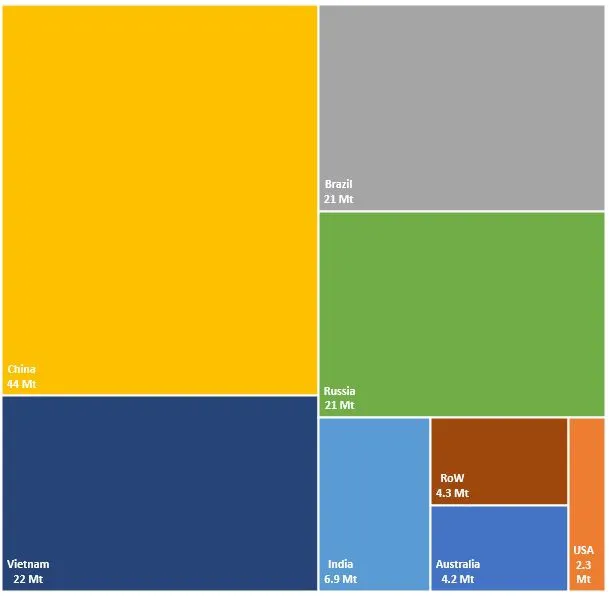
Publicly available data released by exploration and mining companies and published historic data indicate that there are significant global resources and, in some cases, reserves of REEs. The data has been converted to contained rare earth oxides (REOs) to make them comparable. However, due to the lack of available data for the majority of known deposits and operating mines in China, it is difficult to make a true comparison, with China having some of the most significant resources and reserves in the world. Some deposits will have a higher grade of HREE or LREE, depending on the geology of the deposit, but this is, in the majority of cases, indistinguishable from the available public data.
Figure 4 shows the global distribution of REE reserves expressed as tonnes of REO. The rest of the world comprises countries with resources of less than 2 Mt, including Canada, South Africa, Tanzania and Greenland.
Extraction
REEs are extracted from three principal sources:
- hard-rock deposits
- carbonatites
- alkaline igneous rocks
- ion adsorption clays
- heavy mineral sands
Global production from hard-rock deposits is dominated by China. However, there are hard-rock mines outside of China including Mount Weld in Australia, Mountain Pass in the USA and Lovozero in Russia. Production of REEs from ion adsorption deposits is also heavily concentrated in southern Chinese provinces, but recent changes in environmental legislation have prompted Chinese companies to source REEs from similar deposits in Myanmar. Production from heavy mineral sands is dominated by India and Madagascar, but the volume of production is much lower than from other deposit types. Irrespective of deposit type, the global primary supply of REEs is dominated by China and increasingly constrained as Chinese internal demand starts to outstrip domestic supply.
The diversity of REE-bearing deposits requires a variety of mining and processing techniques to be used for their exploitation. The fact that REEs are typically exploited as by-products alongside the extraction of other metals dictates the economics of the operation and the type of mining used. At most mines, beneficiation (processing of the raw ore to remove gangue (uneconomic) minerals) generally occurs on site to produce a REE mineral concentrate that can be shipped for further processing.
Exploitation of unconventional REE-ore minerals (for example, eudialyte, allanite, etc.) will require new methods of beneficiation and processing, as there are currently no commercial-scale processes for REE-bearing minerals other than bastnäesite, monazite, xenotime and loparite. Over the past decade, there has been a marked diversification in global REE supply, with China, which dominated mine production of REOs, dropping its market share from more than 95 per cent in 2010 to 68 per cent in 2020.
Processing
After mining, REE ores are processed to increase their REE content. Initial concentration is normally undertaken at, or close to, the mine site and involves crushing the ore and separating REE-bearing ore minerals from the gangue minerals. This is done using a range of physical processes, such as magnetic separation and froth flotation, depending on the ore type being processed. Chemical processes (for example, calcining and acid leaching) are used to further separate the REEs from their ore minerals.
Separation of the individual REEs from each other is challenging due to their similar chemical properties; however, selective oxidation or reduction and hydrometallurgy — typically ion exchange and solvent extraction — have been successfully employed to separate the individual REEs.
Hydrometallurgical processing is commonly used to separate and purify REEs in three stages:
- dissolution of the REE content in acid, sometimes at elevated pressure and temperature
- separation of the different REEs into pure and concentrated solutions, by solvent extraction or ionic liquid extraction and ion exchange (this is the most difficult part of the whole REE value chain)
- generation of individual and pure REEs
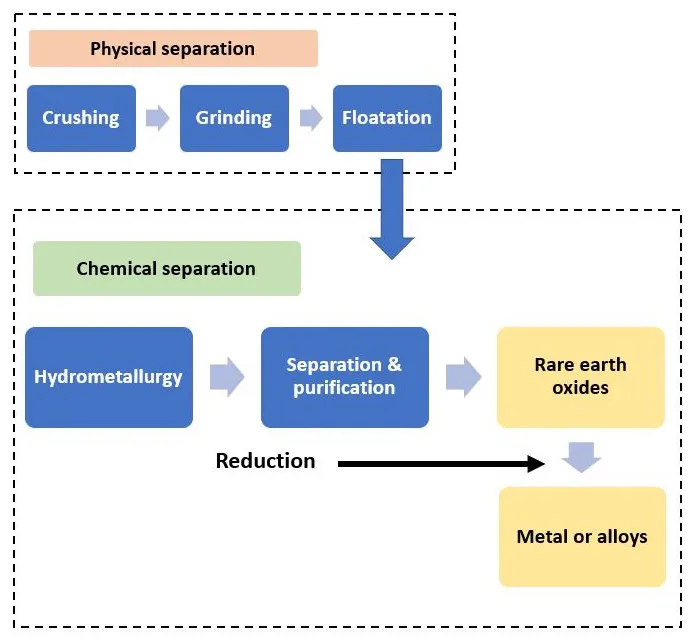
Processing of REE ores and concentrates to produce REE metals and REE chemicals (for example, oxides, carbonates and nitrates) predominantly occurs in China, which accounts for more than 80 per cent of REE processing. However, there is processing capacity in Japan, India, Malaysia and Russia, with REE refining plants also planned in Norway, Sweden, the UK, Canada and the USA (tables 3 and 4).
Country | Company | Product |
---|---|---|
Austria | Treibacher | REE oxides, salts and metal |
China | China Northern Rare Earth Group | REE oxides, carbonates, salts and metal |
China | China Rare Earth Group | REE oxides, carbonates, salts and metal |
Estonia | Silmet | REE metals and alloys |
France | Solvay | REE oxides and organometallics |
India | India Rare Earths | REE chlorides |
India | Toyota Tsusho | REE oxides and carbonates |
Malaysia | Lynas | REE oxides |
Russia | Solikamsk | REE oxides |
Vietnam | Vietnam Rare Earth JSC | REE oxides and metal |
USA | Energy Fuels (offtake for monazite with Neo Performance Materials) | REE carbonates |
USA | MP Materials | REE oxides |
Country | Company | Product |
---|---|---|
Australia | Iluka Resources | REE oxides |
Australia | Northern Minerals | REE carbonates |
Canada | SRC | REE oxides and metal |
Canada | Vital Metals Ltd (offtake agreement with REEtec) | REE oxides |
Norway | REEtec (joint venture with Yara) | REE oxides and nitrates |
Poland | Pulawy (joint venture with Makango) | REE oxides |
Sweden | LKAB | REE oxides |
UK | Peak Resources (offtake agreement with Shenghe) | REE oxides |
UK | Pensana | REE oxides |
USA | Blue Line (joint venture with Lynas) | REE oxides, carbonates, nitrates and acetates |
USA | Texas Mineral Resources (development agreement with USA Rare Earth) | REE oxides |
USA | Ucore | REE oxides |
Drivers and alternatives
Secondary sources
There is a move towards global decarbonisation to tackle climate change, which will lead to increased demand for a range of REEs in the coming decades. As resources of primary REEs are finite and global supply is highly dependent on China, adopting circular strategies, including re-use and recycling, may improve the security of supply of REEs for countries like the UK and alleviate pressure on primary supply.
Products with embedded REEs
REEs play an important role in green and clean energy technologies, including wind turbines, electric vehicles, fuel cells and lighting. Many REEs (for example, Nd, Dy, Pr, Tb) are used in the production of 'NdFeB' (neodymium-iron-boron) magnets. Figure 7 shows the end-use share of NdFeB magnets. These magnets, which are embedded in REE-bearing products, have different lifespans:
- two to three years in consumer electronics
- nine to thirteen years in electric vehicles
- 25 to 35 years in wind turbines
Electric vehicle sales and wind turbine installations have been increasing in the UK during the past few years. Both, therefore, have a high potential of becoming future secondary sources of supply of certain REEs such as Nd, Dy, Pr, Tb. The availability of secondary sources of REEs depends on several factors, including historical production, product lifespan, collection rates and the yields of recycling. When REE-bearing products enter the end-of-life stage, there are many opportunities to retain the highest-value REEs within the UK economy.
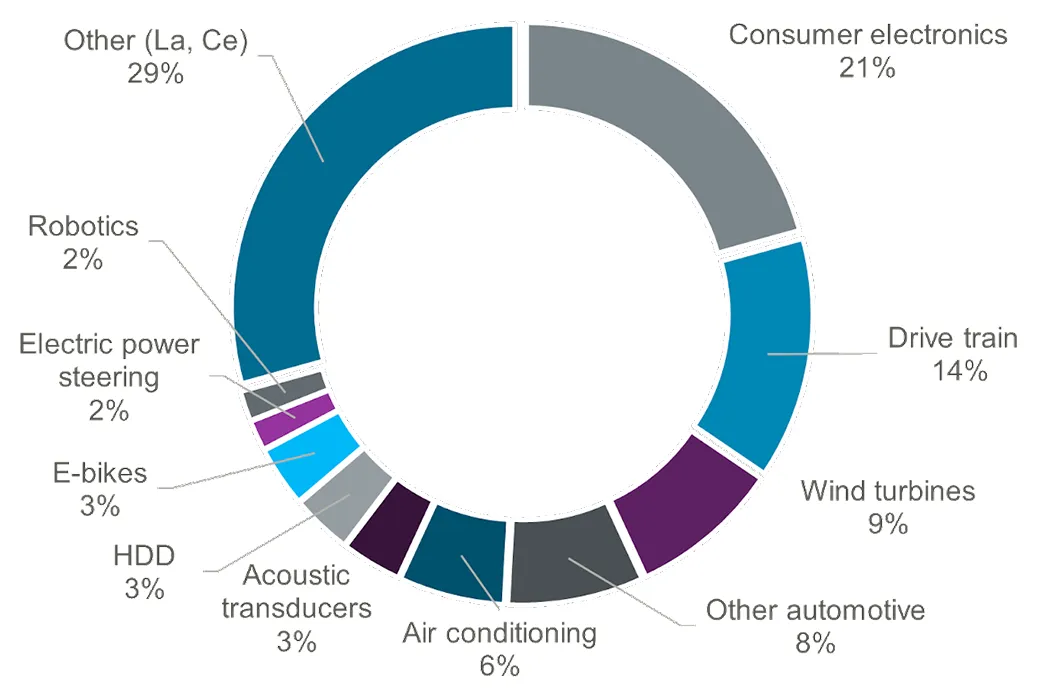
Current situation and challenges
Potential secondary sources of REEs include industry by-products, waste water and end-of-life products. Of these, the end-of-life products have the greatest potential for secondary supply. Since the mid-1980s, NdFeB magnets have been manufactured and widely used, for example in hard disk drives and electric motors. Considering product lifespan, there are already opportunities to recycle the REEs within NdFeB magnets as a secondary supply. However, only 1 per cent of REEs are recovered and less than 1 per cent of NdFeB magnets are recycled.
The main destinations of REE-bearing waste are exports to other countries, landfill sites and loss as contaminants in various waste streams (Figure 2). REEs are technically and economically difficult to collect and recycle because of:
- small quantities of REEs in many applications
- complexity of products
- lack of support for developing novel segregation
- scaling up the recycling processes
In the future, there will be opportunities to recycle REEs from electric vehicles and wind turbines, so it is important to monitor REE flows across the life cycle stages at different levels (substances; components; products) as well as to develop end-of-life management to improve REE supply circularity.
In the near future, there will be rapidly growing demand for REEs but secondary REEs are unlikely to overtake primary supply in the short term. In the long term, developing recycling technologies and infrastructure could contribute to tackling the criticality of REEs. Stock modelling can show the potential quantities available for recycling and highlight the need for future recycling capacity.
Recycling technologies and circular strategies
Currently, there are no effective REE waste collection and separation systems for REE-bearing products. Various recycling technologies to separate and recycle REE are being developed. Table 5 lists the existing recycling and recovery pilot plants and market players, but many of these technologies are still limited to the laboratory or pilot scale and are not yet mature enough to be commercialised. REE-bearing waste could be recycled or recovered into oxide forms or alloy forms, as well as being re-used, repaired, refurbished or remanufactured as secondary components returning to the production process.
The page on circular flows further explains the range of recycling technologies and circular strategies for technology metals that are embedded in different components and end-use products. Different circular strategies will result in varying quality and quantity of secondary REEs, costs and revenue, as well as social and environmental impacts. It is therefore important to consider suitable circular strategies for different REE-bearing products in the UK. This relies on whole-system thinking, not only to determine the trade-offs between these circular strategies and how they may operate in conjunction with each other, but also to understand the effects of secondary REE use in manufacturing new products.
Country | REE recycling pilot plant |
---|---|
Belgium | Solvary SA |
Belgium | Umicore |
Canada | Geomea Resources |
Germany | Osram Licht AG |
Japan | Hitachi Metals, Ltd |
Slovenia | Magneti Ljubljana |
Sweden | STENA Recycling |
UK | Hypromag |
UK | University of Birmingham |
USA | Energy Fuels, Inc |
USA | Global Tungsten & Poweders Corp |
USA | REEcycle, Inc |
Policy intervention
REEs are considered critical mineral resources, therefore several government interventions are needed to support both their primary and secondary supplies. In terms of secondary sources, financial investment is needed in research and development focused on resource efficiency, separation and recycling technologies, as well as infrastructure for the collection and recycling of REE-bearing products.
Collaboration, both globally and domestically, is key to creating diverse primary and secondary REE markets and resilience of both primary and secondary supplies. For example, the Rare Earth Industry Association (REIA) and the European Raw Materials Alliance (ERMA) gather togther REE stakeholders to exchange data, information and knowledge related to REEs. Traceability is particularly significant for creating a circular economy system of REEs. It is important for governments, academia and industry stakeholders across the REE value chain to collaborate in developing a circular economy system and improve the traceability and transparency of REEs.
Education includes training the next generation of skilled workers across the REE value chain, with a focus on the circular economy, whilst educational campaigns for consumers can improve understanding of the social and environmental effects of REEs. Education has the potential to drive social behaviour change to circular use and recycling of REE-bearing products, especially for consumer electronics and electric mobility.
Regulatory intervention can be more powerful in supporting the secondary supply of REEs. The extended producer responsibility (EPR) scheme can enhance not only the producers' responsibility for end-of-life-product management, but also the product design for disassembly, re-use, repair and recycling. Further regulatory issues such as taxes, international trade laws, standardisation, investment and environmental regulations are discussed on the legal and regulatory page.
REEs in the UK
Background geological information and challenges
There are many documented occurrences of REE-bearing minerals in the UK, including:
- allanite
- chevkinite
- fergusonite
- gadolinite
- monazite
- synchysite
However, in most cases, these occurrences comprise only minor, low-tenor REE enrichment over restricted areas. For example, many of these minerals are found as rare accessory phases in some Tertiary granites or are minor accessories to lead-zinc-fluorite mineralisation in the Northern Pennine Orefield (Walters and Lusty, 2011). To date, there has been no mine production of REE-bearing minerals in the UK, nor are there any deposits in which REE reserves or resources have been reported.
There has only been very limited evaluation of the REE potential in the UK. During the early 1990s, BGS made a preliminary assessment of the REE contents of three late-Caledonian, alkaline intrusive complexes in north-west Scotland. Rock and drainage samples from Loch Borralan, Loch Ailsh and Loch Loyal were analysed for cerium, lanthanum and yttrium (Shaw and Gunn, 1993). BGS also undertook an assessment of the economic potential of mudstone-hosted nodular monazite in south-central Wales during this period (Smith et al., 1994). More recently, a BGS-hosted MSc student reappraised drill core from the ultramafic section of the Loch Borralan complex to further assess its potential as an REE resource (Griffith, 2011) and, in 2013, BGS studied the formation of late-stage, allanite-bearing veins associated with the Loch Loyal syenite complex (Hughes et al., 2013; Walters et al., 2013).
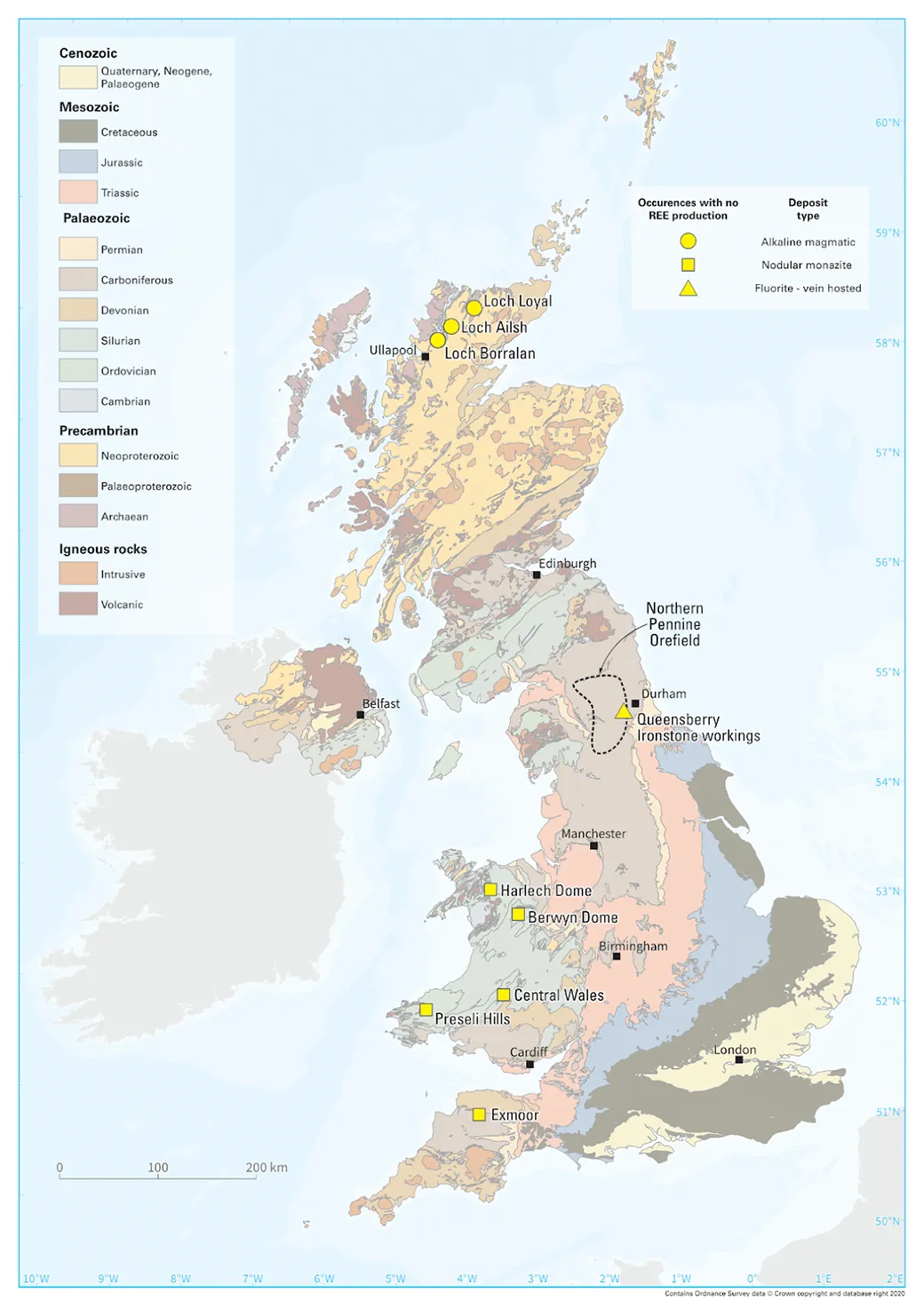
A priority target for further investigation is the Cnoc nan Cuilean Intrusion in north-west Scotland. The hydrothermal, allanite-bearing veins that cross-cut the intrusion contain the highest REE grades recorded in the UK (up to 2 wt% TREO) (Walters et al., 2013). The known occurrence of significant hydrothermal, REE-mineralised veins associated with alkaline igneous rocks elsewhere in the world provides a strong basis for evaluating this area further. However, there is currently no commercial process for extracting REEs from allanite; this, coupled with the thin and discontinuous nature of the veins, makes them unlikely to be economic.
It is also important to note that previous work by BGS on the Caledonian alkaline intrusions of north-west Scotland has focused on the platinum group metal potential of six selected parts of these bodies. Systematic investigations over the entirety of these complex intrusions are recommended in order to fully evaluate their REE potential.
UK critical minerals strategy and market opportunities
A recent UK criticality assessment published by BGS, commissioned by BEIS (now DBT), shows REEs high on the list. The security of a rare-earth material supply is crucial to the UK's electrification ambitions, which are required to meet the UK Government's net zero target. The UK's Critical Minerals Strategy, announced in 2022, aims to accelerate the growth of the UK's domestic capabilities, collaborate with international partners and enhance international markets to make them more responsive, transparent and responsible. There are significant opportunities for the UK to deploy its expertise and forefront research assets for innovation in these areas and establish REE market share.
To build up the sustainable supply chain of REEs in the UK, the UK would need to diversify its supply of REEs and explore the possibility of mining and refining ores into metals and alloys. The UK has a leading role in research and development, education of metal refining and green chemistry. It is therefore important to use this strength to develop new innovations for the chemical treatment and separation of REEs. Furthermore, there are many UK-based original equipment manufacturers; it is also suggested that incentives are provided for them to develop magnet production and its end-of-life management.
Recycling of REE-containing magnets and products for secondary supply
The UK will need to secure significant quantities of REEs to achieve the electrification transition. There are supply risks and limits for domestic primary production. It is therefore crucial to develop a long-term ecosystem for secondary supply. The current in-use stocks could provide buffer capacity if circular economy systems are established. In the future, assuming that the net-zero targets materialise, the UK stock in products could create viable circular economy business opportunities.
As most of the current plants are still at the pilot scale, it is necessary to assess the technology readiness levels (TRLs) of the UK's existing REE recovering technologies. The UK has expertise and capability in material science and REE recycling; for example, the University of Birmingham has strong research expertise in recovering REE. Investing in research and development and establishing a secondary supply chain could expand the REE recycling capacity of the UK and stimulate further innovation in magnets, especially research into next-generation magnet materials.
More information
References
Idoine, N E, Raycraft, E R, Shaw, R A, Hobbs, S F, Deady, E A, Everett, P, Evans, E J, and Mills, A J. 2022. World Mineral Production 2016–2020. (Nottingham, UK: British Geological Survey. Available from https://nora.nerc.ac.uk/id/eprint/534464/
IRENA (2022) (REE demand in 2020 by end-use sector)
Deady 2021 (map of occurrences)
USGS (2023) (Global distribution of REE reserves)
Smith et al. (2017) (REE processsing)
Walters and Lusty, 2011 (REEs as minor accessories to lead-zinc-fluorite mineralisation in the Northern Pennine Orefield)
Shaw and Gunn, 1993 (Rock and drainage samples from Loch Borralan, Loch Ailsh and Loch Loyal were analysed for cerium, lanthanum and yttrium)
Smith et al., 1994 (BGS also undertook an assessment of the economic potential of mudstone-hosted nodular monazite in south-central Wales
Griffith, 2011 (the ultramafic section of the Loch Borralan Complex to further assess its potential as a REE resource)
Hughes et al., 2013 (late-stage, allanite-bearing veins associated with the Loch Loyal Syenite Complex)
Walters et al., 2013 (late-stage, allanite-bearing veins associated with the Loch Loyal Syenite Complex)
Shaw and Gunn (2020) (Location of the principal REE occurrences in the UK)
Further reading
Alves Dias, P, Bobba, S, Carrara, S, and Plazzotta, B. 2020. The role of rare earth elements in wind energy and electric mobility. (Luxembourg: Publications Office of the European Union. DOI: 10.2760/303258
Binnemans, K, McGuiness, P, and Jones, P T. 2021. Rare earth recycling needs market intervention. Nature Reviews Materials, Vol. 6, 459–461. DOI: 10.1038/s41578-021-00308-w
Jyothi, R K, Thenepalli, T, Ahn, J W, Parhi, P K, Chung, K W, and Lee, J Y. 2020. Review of rare earth elements recovery from secondary resources for clean energy technologies: Grand opportunities to create wealth from waste. Journal of Cleaner Production, Vol. 267, 122048. 10.1016/j.jclepro.2020.122048
Patil, A B, Paetzel, V, Struis, R P W J, and Ludwig, C. 2022. Separation and recycling potential of rare earth elements from energy systems: feed and economic viability review. Separations, Vol. 9(3), 56. DOI: 10.3390/separations9030056
Walton, A, Anderson, P, Harper, G, Mann, V, Beddington, and 18 others. 2021. Securing technology-critical metals for Britain (pdf). (Birmingham, UK: University of Birmingham.)
The UK's Critical Minerals Strategy.
UK supply chain opportunity in materials for permanent magnets (pdf).