The lithium market is rapidly developing because of the global focus on decarbonisation technologies, in particular the electrification of transport and the development of energy storage solutions. The increasing demand for lithium-ion batteries in electronic devices is another driver.
Lithium is used in a number of applications, including:
- batteries
- ceramics and glass
- polymers
- lubricating greases
- air treatment
The dominant end-use of lithium is in batteries, which accounted for a 71 per cent market share in 2018. The second-most important use (in terms of market share) is in ceramics and glass, which accounted for 14 per cent of the market in 2018 (Figure 1).
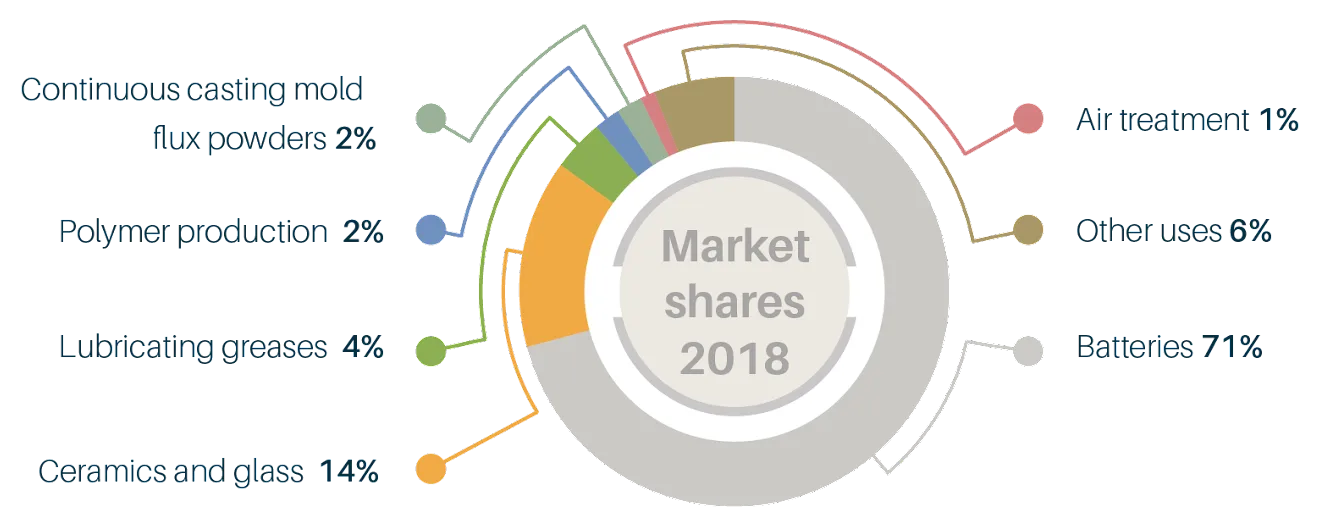
Acquiring lithium
Supply chain
Lithium supply chains are complex and commonly global in their extent, with steps that include:
- exploration
- mining
- processing
- manufacturing
- use
- end-of-life
Lithium as a raw material is sourced either as a mineral, predominantly spodumene, or as brine. Although lithium is available from a variety of different sources, the processing and production of compounds is currently concentrated in China.
Due to high projected demand in the battery sector, the supply chain is expanding very rapidly at present. The rapid supply chain developments in Tier 1 (original equipment manufacture) and Tier 2 to 3 (cathode and battery manufacture) have an impact on Tier 4 (raw materials) of the supply chain, with new exploration and mining projects, but have a different response pace.
The short- to medium-term outlook for lithium is that of rapdily increasing demand for all markets, but especially for the manufacutre of lithium-ion batteries for electric vehicles.
The challenges associated with bringing new supply on stream are many and varied, and go beyond the physical imbalance between supply and demand. Environmental, economic, social and political challenges can be significant and may strongly influence future lithium supply across the whole supply chain.
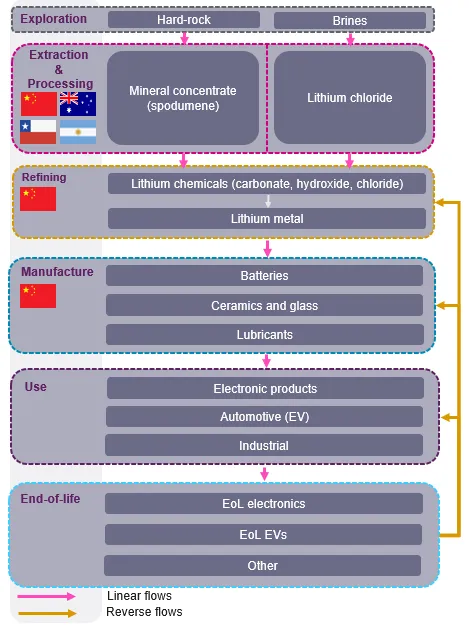
Exploration
Exploration for lithium has rapidly expanded as a result of both rising demand and the predicted increase in future demand, with some forecasts suggesting metal requirements in 2050 will be around 2100 per cent higher than overall use in 2020 (KU Leuven, 2022).
There are currently more than 300 lithium exploration projects at varying stages of development (exploration; pre-feasibility; feasibility; construction). The majority of these projects are located in Australia, Canada, Argentina and the USA. However, it is likely that many of the projects will not receive the investment required to become operating mines.
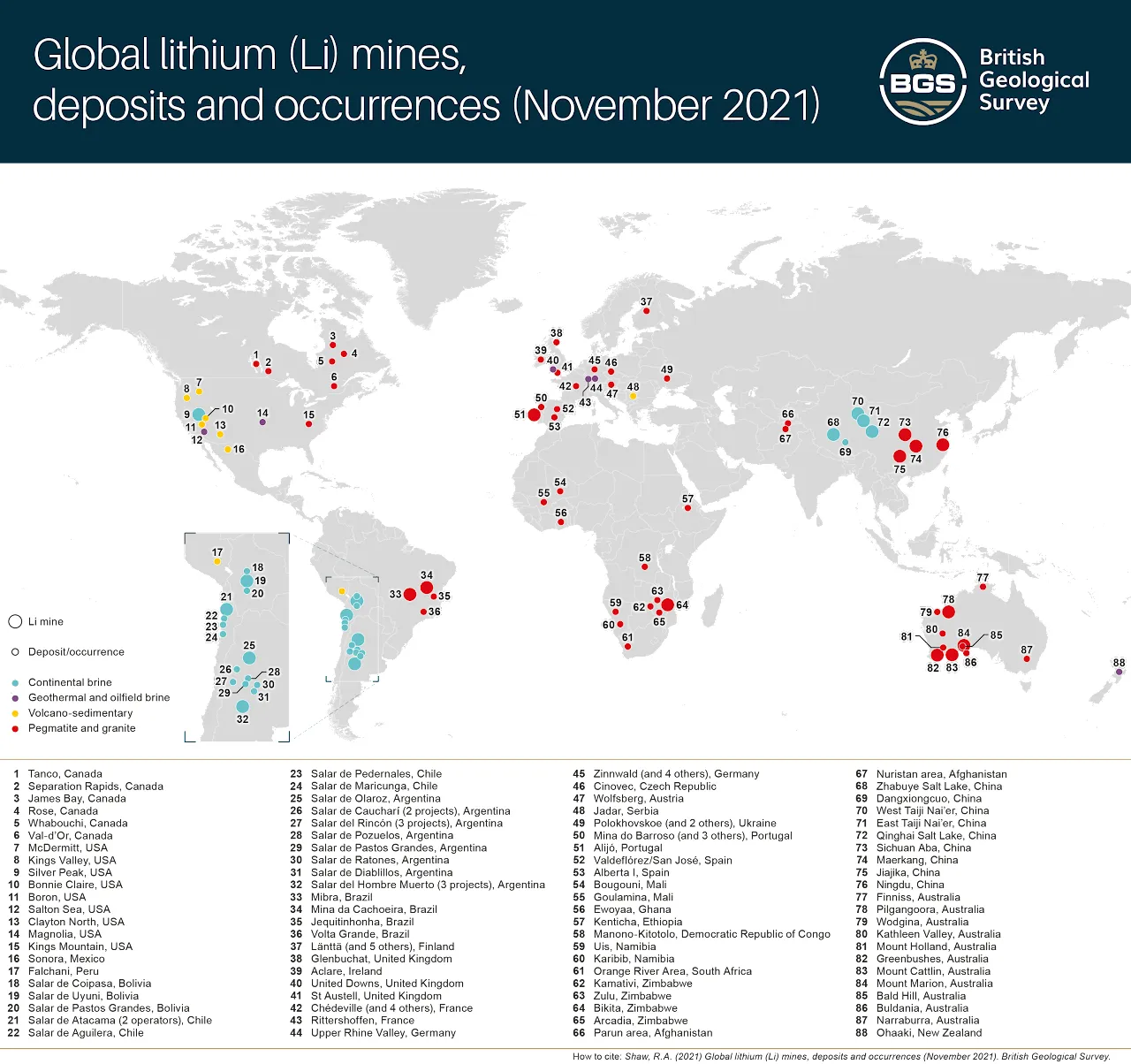
Lithium-bearing mineral resources are known across the globe, occurring in a range of deposit types in a variety of geological settings (Figure 3). However, lithium is principally extracted from two types of mineral deposit: hard rocks and brines. Table 1 is an overview of the charateristics of hard rock and brine-hosted lithium deposits.
In terms of hard rock deposits, lithium is chiefly extracted from lithium aluminosilicate minerals such as spodumene and petalite, which are found in pegmatites. Other lithium-bearing minerals, for example hectorite (a lithium-rich clay) and jadarite (a lithium borosilicate) are not currently exploited on a commercial scale but may become important sources of lithium in the future. There is also increasing interest in recovering lithium from lepidolite and zinnwaldite, lithium-bearing micas that are typically found in hard rock deposits.
Lithium extraction from brines is principally from continental brine deposits, such as the salt lakes and salt pans of the central Andes in South America.
The extraction of lithium from geothermal and oilfield brines, although technically feasible, is not currently taking place but may become important in the future (Brown, 2016).
Deposit type | Description | Typical grade | Examples | |
---|---|---|---|---|
Hard rock | Pegmatites | Coarse-grained igneous rock formed during late-stage crystallisation of magmas | 1.5 to 4% Li2O |
|
Hard rock | Hectorite | Lenses of smectite clay in association with volcanic centres | 0.4% Li2O |
|
Hard rock | Jadarite | Altered sediments in an enclosed basin | 1.5% Li2O |
|
Brine | Continental | Salt pans or salars in enclosed basins with lithium enrichment likely to be from hot springs | 0.04 to 0.15% Li |
|
Brine | Geothermal | Elevated levels of lithium contained in steam at geothermal power stations | 0.01 to 0.035% Li |
|
Brine | Oilfield | Elevated levels of lithium contained in waters or brines produced in oilfields | 0.01 to 0.05% Li |
|
Resources and reserves of lithium
Data held by the United States Geological Survey (USGS) indicate there are significant global resources and reserves of lithium. Global resources of lithium are currently estimated to be about 183 million tonnes (Mt), whilst reserves are estimated to be about 26 Mt.
Although distributed across the globe, a significant proportion (more than 80 per cent) of lithium resources are found in only five countries:
- Argentina
- Australia
- Bolivia
- Chile
- USA
A similar concentration is seen in the distribution of lithium reserves, with only four countries accounting for more than 70 per cent of global reserves (Figure 5):
- Argentina
- Australia
- Chile
- USA
The majority of lithium resources and reserves in Chile, Argentina and Bolivia are associated with continental brines, whilst in the USA and Australia they are dominated by hard rock-hosted lithium resources and reserves.
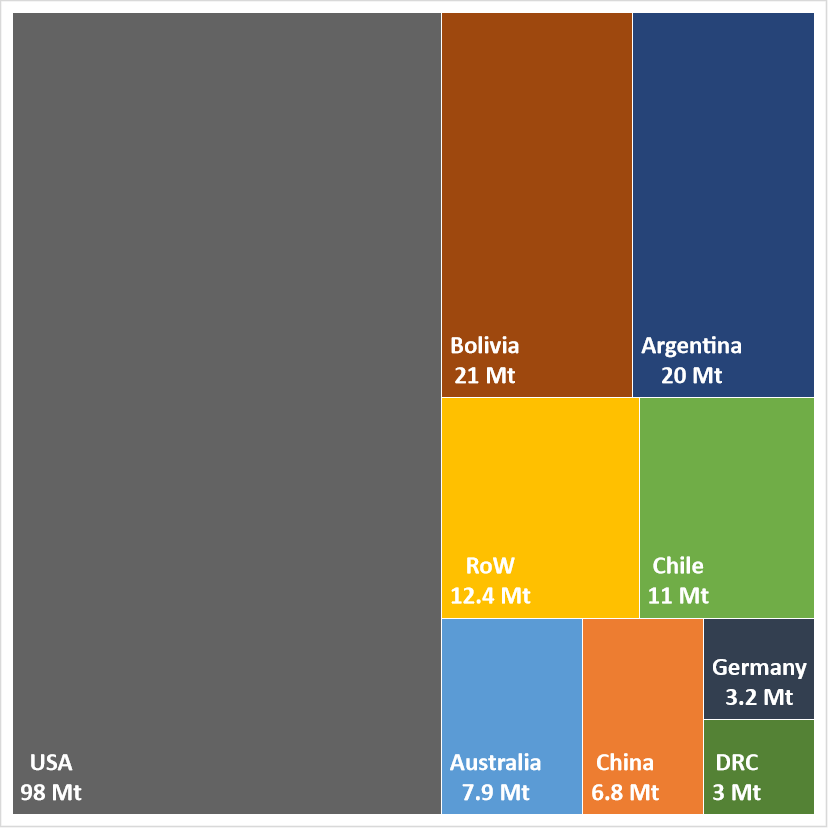
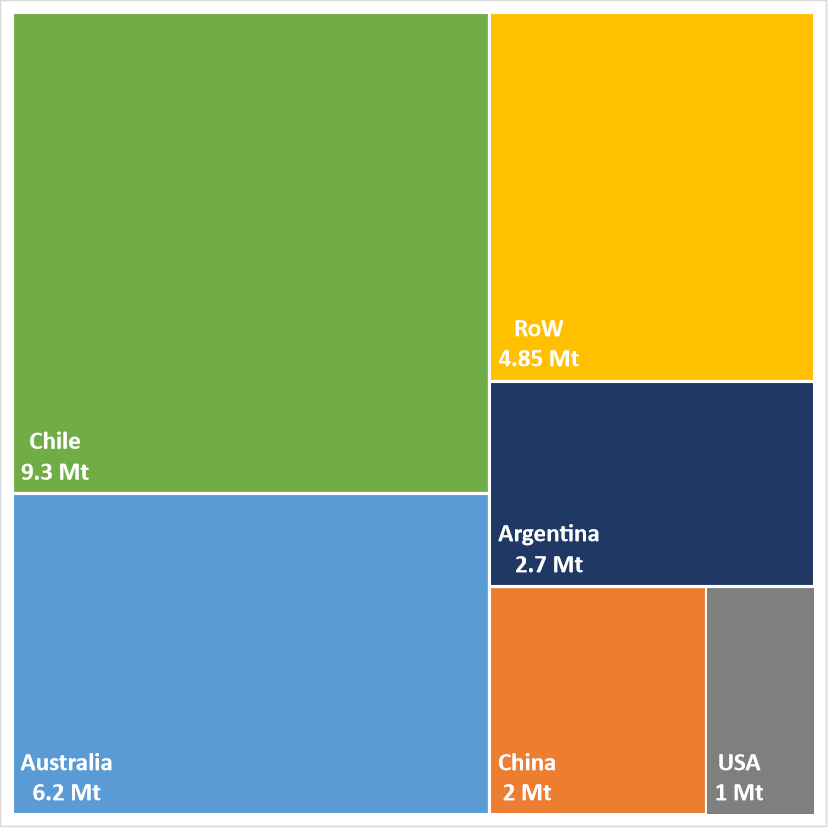
Extraction
Lithium is chiefly extracted from two types of mineral deposit: hard rock deposits (pegmatites) and brines (continental brines).
Hard rock deposits are typically mined using similar techniques to many other metals, using surface (open pit) or subsurface (underground) methods, whilst brines are liquids and therefore extracted from wells by pumping.
Hard-rock lithium deposits that are near the surface, usually at a depth of less than 100 m, are mined using open-pit mining methods. These generally involve removing overburden (unmineralised soil and rock), digging out the ore or blasting it with explosives, then removing it by truck or conveyor belt for stockpiling prior to further processing. Underground mining methods are used when surface mining methods become too expensive, for example when a deposit is buried too deeply. Initially, an adit (horizontal), shaft (vertical) or decline (at an angle) will be sunk to access the buried deposit and the ore is mined using explosives and specialist mining equipment. It is then transported to surface for processing using trucks, conveyor belts or underground rail systems.
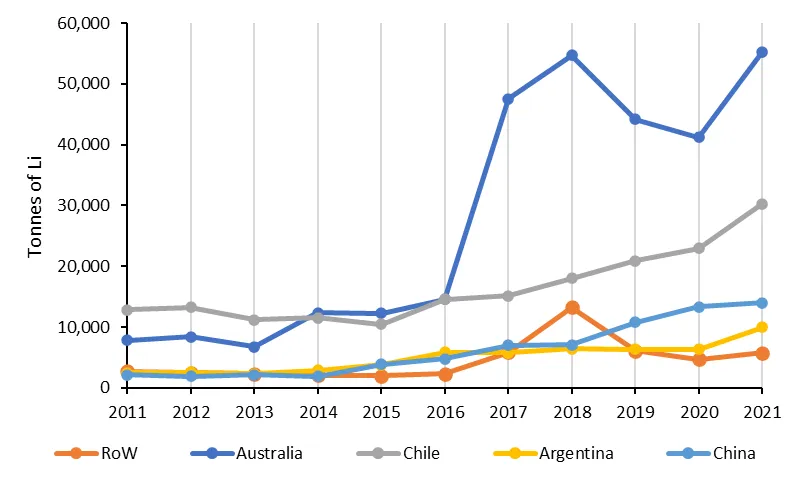
During the past decade, global production of lithium has been fairly evenly split between extraction from hard rock deposits (around 37 to 65 per cent) and extraction from continetal brines (around 35 to 63 per cent). However, since 2016, production from hard rock sources has dominated. During this time, production of lithium has increased significantly from almost 28 000 tonnes in 2011 to more than 115 000 tonnes in 2021 (go to Figure 1 for an overview of lithium demand in 2018). Australia and Chile have been the dominant producers during this period, together accounting for more than 70 per cent of the global total each year. Mine production from China, Argentina and the rest of the world has also generally increased during this time, although at a slower rate compared to Chile and Australia.
Processing
Processing routes for lithium will largely depend on the characteristics (for example, mineralogy) of the deposit being exploited. For example, lithium recovered from brines is subject to a very different set of processes to lithium recovered from hard rock sources.
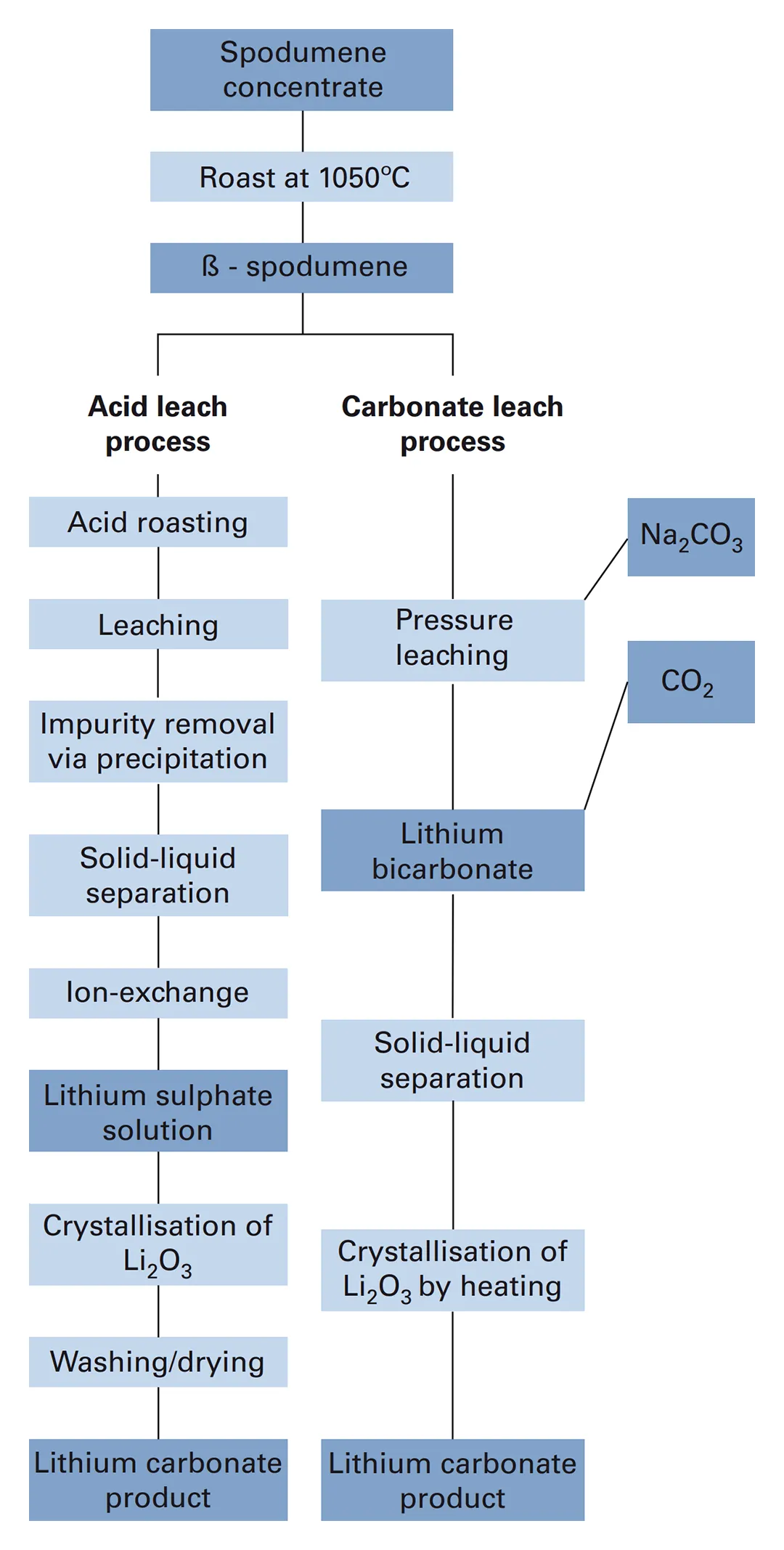
Hard rock
After mining, lithium-bearing minerals (predominantly in the form of spodumene) are processed to increase the lithium content. This stage of initial concentration is generally performed at or near to the mine site and involves crushing the ore and separating the lithium-bearing ore minerals from the gangue (uneconomic) minerals, using a range of physical processes like gravity separation, magnetic separation and froth flotation. Chemical processes, such acid roasting and leaching, are used to separate the lithium from the ore minerals and to remove unwanted impurities like iron. A series of chemical steps are then used to produce high-purity lithium carbonate (Figure 7).
Processing of lithium ores and concentrates predominantly takes place in China, where high-purity lithium chemicals such as lithium carbonate (Li2CO3) and lithium hydroxide (LiOH) are produced chiefly for the manufacutre of batteries. However, lithium refining also takes place, albeit on a smaller scale, in Chile (Li2CO3 and LiOH), Argentina (LiOH and LiOH) and Europe (LiOH), with future refining capacity planned in Australia (LiOH).
There is currently no commercial extraction of lithium from clay (hectorite)-bearing deposits nor from lithium-bearing micas (for example, lepidolite); however, feasibility studies have shown this may be possible in the future, if the technologies can be scaled up.
Brines
After extraction, ususally by pumping, the brine undergoes an initial stage of concentration to increase the lithium content. This is usually achieved by solar evaporation in a series of surface ponds. Lithium is highly soluble, therefore other compounds such as sodium chloride, potassium chloride or calcium sulphate will precipitate first, leaving the brine increasingly concentrated in lithium. The lithium itself will eventually precipitate, typically as lithium chloride. The concentrated brine is further processed to remove impurities such as magnesium and boron. The resulting lithium chloride is reacted with sodium carbonate to precipitate a lithium carbonate slurry that is filtered, washed and dried to produce lithium carbonate with more than 99 per cent purity. After the extraction of lithium, brine is re-injected into the salar (Figure 8).
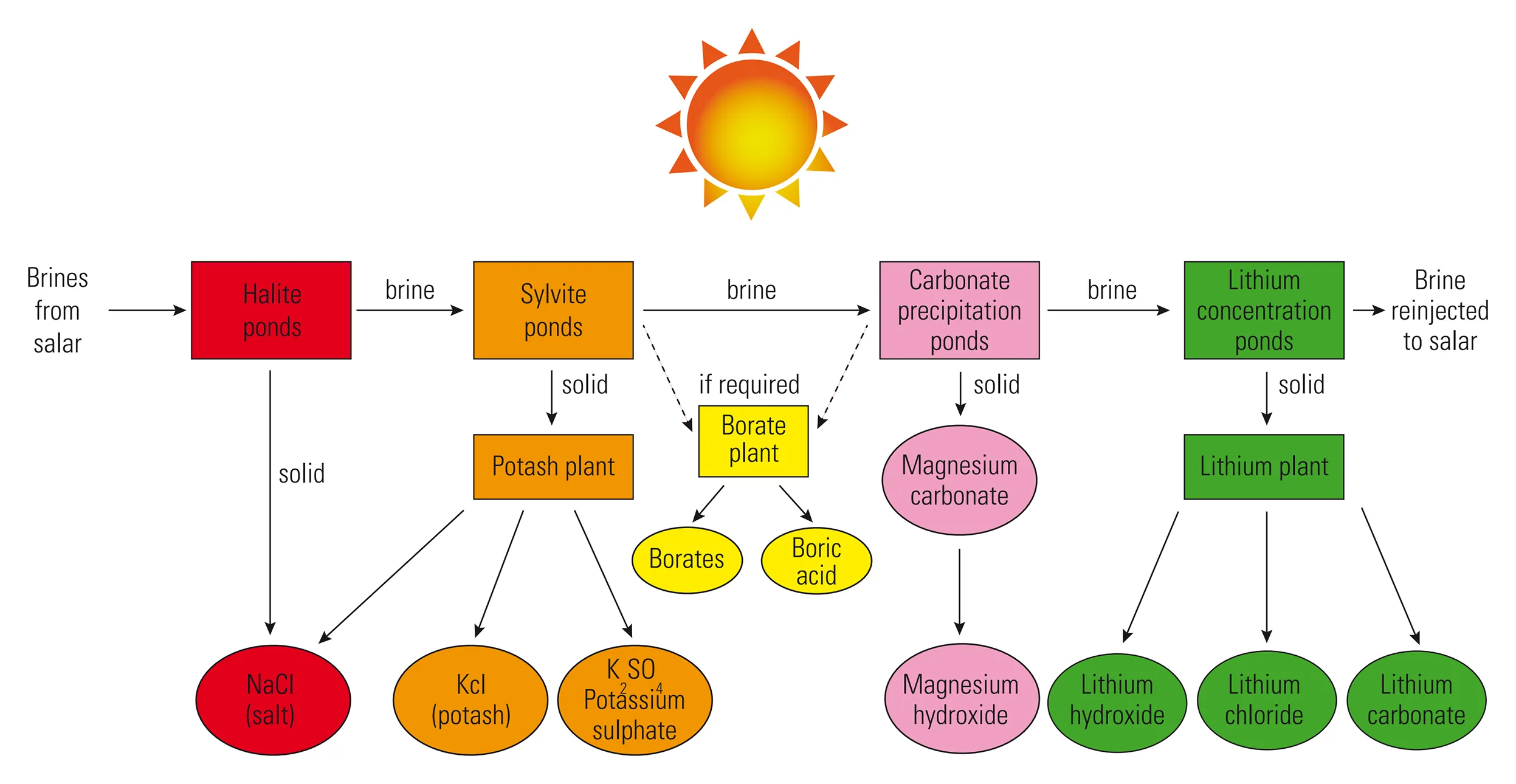
Emerging technology
Direct lithium extraction (DLE) is an emerging technology for fast processing of lithium, especially lithium extracted from brine deposits. The technology is a form of ion exchange where lithium (green circles in Figure 9) is selectively extracted from a brine using a lithium-selective sorbent (orange hexagons in Figure 9). The brine passes through a tank and mixed with the sorbent. The lithium-enriched brine then passes into a second tank for further refining, whilst the unwanted brine, now rich in impurities like sodium, magnesium and calcium, is re-injected (Figure 8).
DLE simultaneously increases the lithium content of the brine and removes unwanted impurities. DLE may prove particularly useful where the lithium grade in the brine is low (ten to hundreds of parts per million). The environmental impact of DLE is lower than other processing technologies, as it typically requires less energy, less water and has a smaller physical footprint. However, complex brine chemistry can increase the time required to establish a system, so increased testwork may be required, ongoing expenditure may be higher and there may be technical risks associated with re-injection of brine.
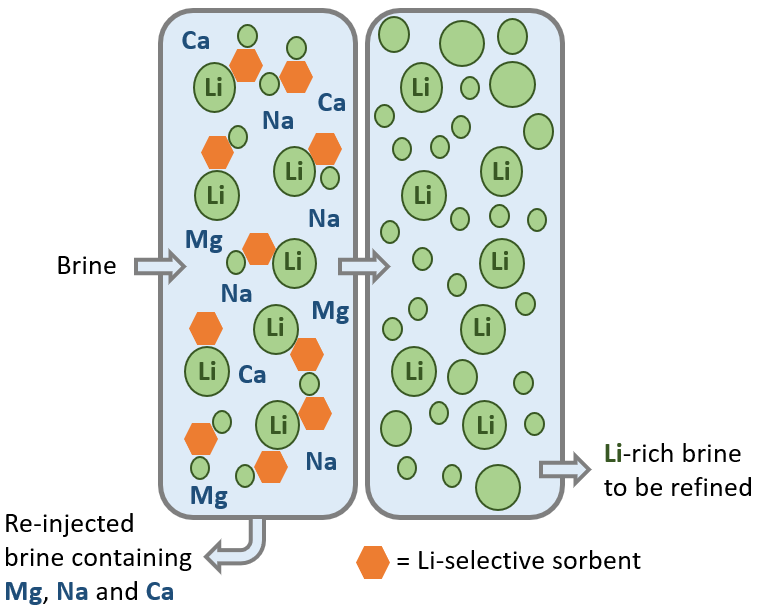
Drivers and alternatives
Secondary sources
As demand for lithium is forecast to rise sharply in the short to medium term, recycling and re-use will become increasingly important parts of the supply chain. However, some end-use applications of lithium, for example glass, ceramics and lubricants, are dispersive uses; recovery of lithium from these secondary sources is unlikely to be important in the future. Lithium-ion batteries are more promising for both re-use, remanufacturing and recycling, although this is not currently happening at a large scale.
Re-use
Re-use of lithium-ion batteries typically takes two forms: direct re-use (where the battery remains intact) and indirect re-use (where some remanufacturing is required, such as only re-using the cathode). The re-use of lithium-ion batteries can also be considered in terms of whether the battery is used in the same application (primary re-use) or in a different application (secondary or tertiary re-use). An example of direct secondary re-use would be using an end-of-use electric vehicle battery for domestic energy storage.
Re-use has its limitations, however, with second-life batteries typcially needing to be used in less-demanding applications such as domestic energy storage. Additionally, the battery design may not allow for re-use; for example, assembly methods that rely on glues and adhesives to bond cells can make future repair or re-use impossible if a single cell fails in the battery pack, meaning the whole pack will need to be replaced. There are also concerns around the safe re-use of lithium-ion batteries, where there are typically very few or no codes or standards related to the regulation of second-life applications. For example, there are currently no standards focused on the testing of second-life batteries (Harper et al., 2023).
Recycling
Processes for recycling lithium-ion batteries exist, although the focus is largely on recovery of the higher-value metals, such as cobalt, manganese and nickel. Recently, there has been a great deal of research interest in lithium-ion battery recycling, with a particular focus on the recovery of lithium.
There are three principal routes for lithium-ion battery recycling:
- pyrometallurgy
- hydrometallurgy
- mild recycling
Pyrometallurgy is fairly rapid process that is easy to scale up. It also has the benefit of being able to accept a range of different battery chemistries. However, the high temperatures used during the process can generate significant emissions such as carbon dioxide, carbon monoxide and sulphur dioxide, which require treatment and therefore increase the operating costs. The energy consumption is also very high. Lithium is not easily recovered, as it usually ends up in the slag (Liu et al., 2019).
Hydrometallurgy is a complex process that relies heavily on the use of inorganic acids, organic acids and alkaline solutions. It can be a costly process, as set-up times can be long and there is a requirement to treat waste water and spent reagents, which further adds to the cost. On the plus side, all metals, inlcuding lithium, can be recovered using hydrometallurgical methods that result in the precipitation of high-purity compounds, although reported ltihium recoveries are not as high as for other metals (Liu et al., 2019).
Mild recycling methods, for example carbothermal reduction or sulphation roasting, typically use less energy and have generally good recycling efficiencies. Lithium can also be recovered using these methods. However, like pyrometallurgy, these processes produce gaseous emissions that need to be treated (Liu et al., 2019).
Future direction
There are many opportunities for recycling of lithium-ion batteries. However, a great deal of research is still required to optimise processes for the recovery of lithium in a safe and cost-effective manner. Similarly, there is scope for re-use of lithium-ion batteries in secondary appliactions, although concerns around safety and regulation need to be addressed. In both cases, academia, industry and governments will need to collaborate to realise these opportunities in the future.
Policy intervention
Lithium is considered a critical raw material. This means that several government interventions are needed to support both the primary and secondary supply of lithium. In terms of secondary sources, financial investment is needed in research and development focusing on resource efficiency, separation and recycling technologies, as well as infrastructure for the collection and recycling of lithium-ion batteries.
Collaboration, both globally and domestically, is key to creating diverse primary and secondary lithium markets and developing resilience in both primary and secondary supply. For example, the International Lithium Association (ILiA) gathers together lithium stakeholders to exchange data, information and knowledge related to lithium. Traceability is particularly significant for creating a circular economy system of lithium. It is important for governments, academia and industry stakeholders across the lithium value chain to collaborate in developing such a system and improve the traceability and transparency of lithium.
Education includes training the next generation of skilled workers across the lithium value chain, with a focus on the circular economy, whilst educational campaigns for consumers can improve understanding of the social and environmental impacts of lithium. Education has the potential to drive social behaviour to change to circular use and recycling of lithium-bearing products, especially for consumer electronics and electric mobility.
Regulatory intervention can be more powerful in supporting both primary and secondary supplies. Regulatory measures that facilitate responsible domestic exploration and extraction could make a significant contribution to improving primary supply. Unlocking the potential of domestic geological resources would not only help build self-sufficiency in lithium supplies, but would also reduce the need to transport lithium across long distances, thus reducing the overall carbon footprint of products containing lithium.
Equally important in ensuring a secure supply chain is investment in infrastructure for midstream processing. Secondary supplies can be enhanced by robust policies that ensure sustainable end-of-life management of products containing lithium, so that critical materials are returned back to the value chain. Sound extended producer responsibility frameworks will be imperative, along with robust and focused collection and recovery targets for lithium.
Such circular economy strategies aid producers' responsibility for end-of-life product management, but also encourage product design for disassembly, re-use, repair and recycling.
Role of regulation and policy
Regulatory intervention can be powerful in supporting both primary and secondary supplies of lithium. The UK has identified geological resources of lithium in regions such as Cornwall, but accessing these domestic resources requires fit-for-purpose regulatory frameworks. Measures that facilitate responsible domestic mining (such as integrated, thoughtful planning and permitting regimes for exploration and extraction) would significantly improve primary supply. This would not only help the UK achieve greater self-sufficiency in lithium supplies, but would also reduce the need to transport minerals across long distances, thus reducing the overall carbon footprint of products containing lithium.
Equally important is the need to build domestic capabilities in midstream processing: without this, there is a significant risk that valuable critical minerals are lost overseas and never return to the domestic value chain.
Reducing planning and licencing times for extraction and midstream processing as well as reducing energy costs can make a significant contribution.
Further regulatory issues such as taxes, international trade laws, standardisation, investment and environmental regulations are discussed on the legal and regulatory page.
Focus on the UK
In the UK, lithium primarily occurs as a minor element in mica found in granite and granite pegmatites, especially in south-west England. In fact, lithium-bearing mica was first identified in the St Austell Granite in south-west England in 1825. During the 19th century, a small amount of lithium-bearing mica was extracted from the Trelavour Downs pegmatite within the St Austell Granite, for use in firework manufacturing (Hawkes et al., 1987). This working is the only known site of lithium extraction in the UK.
To date (November 2023) there has only been limited evaluation of the lithium potential in the UK. During the 1980s, BGS undertook an assessment of the potential to recover lithium from mica in the St Austell Granite (Hawkes et al., 1987). Since 2017, two exploration companies (Cornish Lithium Ltd and British Lithium Limited) have started exploring for lithium in south-west England. Furthermore, the Li4UK project has recently (August 2019) undertaken systematic lithogeochemical sampling at various sites across the UK, with the aim of evaluating domestic lithium resources (Li4UK, 2019).
There is currently no mine production of lithium in the UK and there are no deposits in which lithium reserves or resources have been reported.
Even though other lithium minerals, such as amblygonite, spodumene, petalite, montebrasite and elbaite, are known to occur in the UK, many of them are very rare and have only been documented at a few localities in the UK (Tindle, 2008).
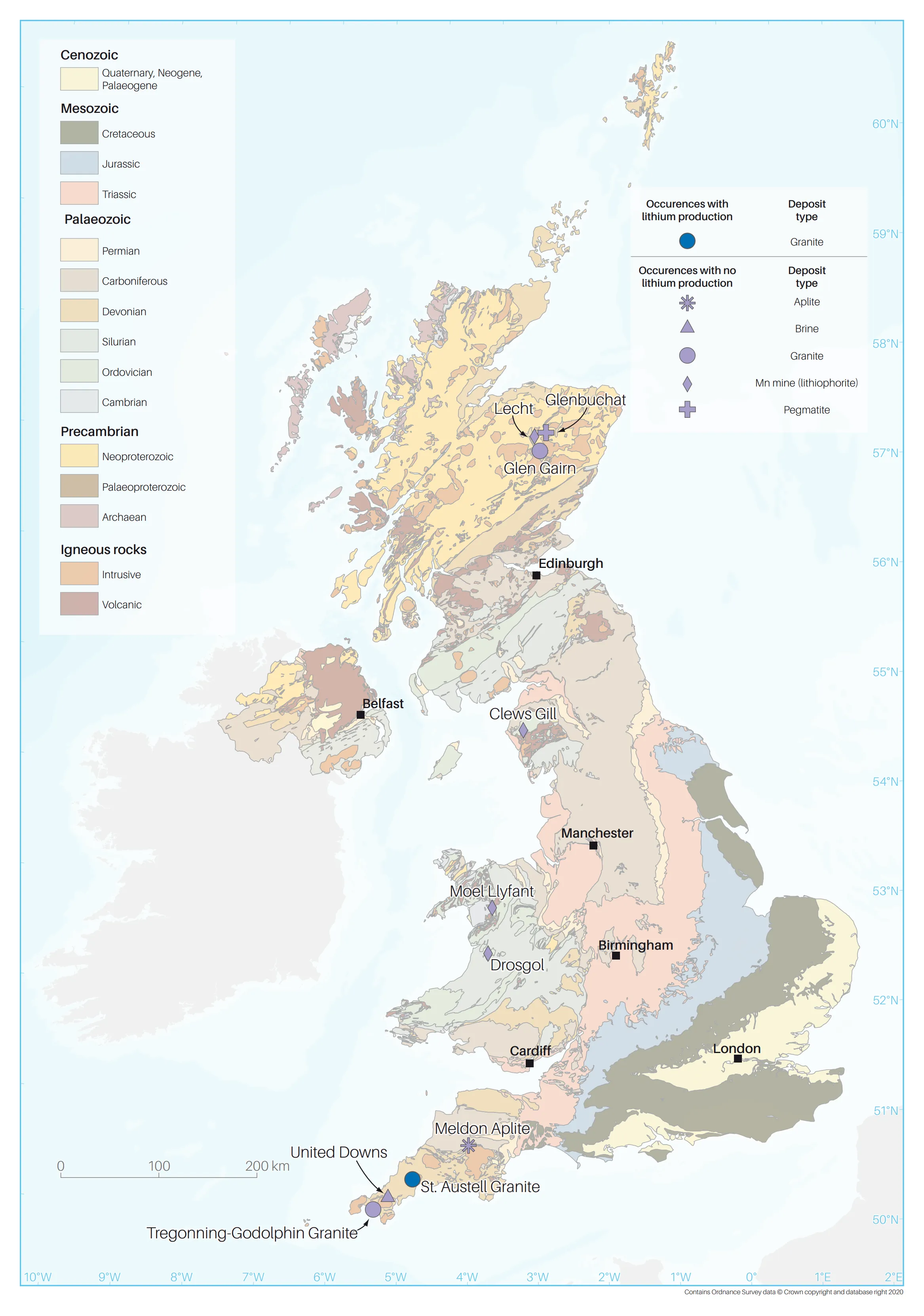
Systematic exploration for lithium in the UK has been extremely limited, although there was a significant increase in research and commercial exploration for lithium in 2018 and 2019. This was most notable in south-west England, where ongoing exploration aims to sample geothermal waters to measure their lithium content. This will provide new data that are necessary to assess the resource potential and the feasibility of commercial extraction. Until a mineral resource estimate and the results of metallurgical testing of samples are published, there is also uncertainly about the resource potential of hard-rock lithium deposits in south-west England. Weardale Lithium Ltd is also assessing the lithium potential of geothermal brines associated with the Weardale Granite in north-east England.
A priority target for further investigation is the buried spodumene-bearing pegmatite at Glenbuchat in north-east Scotland. The minerals present in the Glenbuchat pegmatite — spodumene, lepidolite, manganotantalite, manganocolumbite and elbaite (Tindle, 2008; Starkey and McMullen, 2017) — and its extreme enrichment in rubidium, lithium, caesium and tantalum (Shaw and Goodenough, 2013) are indicative of a highly evolved lithium-caesium-tantalum (LCT) pegmatite. The known enrichment of lithium in similar LCT pegmatites elsewhere in the world provides a strong basis for evaluating this site further.
The other target worthy of further investigation is the lithium-mica-bearing area of the St Austell Granite. Hawkes et al. (1987) estimated there to be about 3.3 million tonnes of lithium in the St Austell Granite; however, this figure could be higher as the estimate was based on an 'assumed' deposit thickness of 100 m.
UK critical minerals strategy and market opportunities
A recent UK criticality assessment published by BGS and commissioned by the (former) Department for Business, Energy and Industrial Strategy shows lithium as being of high potential criticality to the UK (Lusty et al., 2021). The security of lithium supply is crucial to the UK's electrification of transport ambitions that are required to meet the UK Government's net zero target.
The UK's critical minerals strategy, announced in 2022, aims to:
- accelerate the growth of the UK's domestic capabilities
- collaborate with international partners
- enhance international markets to make them more responsive, transparent and responsible
There are significant opportunities for the UK to utilise its expertise and cutting-edge research assets for innovation in these areas and establish lithium market share.
To create a sustainable supply chain for lithium in the UK, the UK would require diversification of the supply of lithium whilst also exploring the possibility of domestic mining and refining of ores and secondary materials into lithium metal and lithium compounds. The UK has a leading role in research and development, education in metal refining and green chemistry. Therefore, it is important to play to the UK's strengths in developing new innovations for the lithium market (for example, battery technology and recycling). Furthermore, there are many UK-based original equipment manufacturers, so it will be important to provide incentives for them to develop battery production facilities and engage in the end-of-life management of batteries.
More information
References
Harper, G D J, Kendrick, E, Anderson, P A, Mrozik, W, Christensen, P, and 60 others. 2023. Roadmap for a sustainable circular economy in lithium-ion and future battery technologies. JPhys Energy, Vol. 5, 021501. DOI: 10.1088/2515-7655/acaa57
Liu, C, Lin, J, Cao, H, Zhang, Yi, and Sun, Z. 2019. Recycling of spent lithium-ion batteries in view of lithium recovery: a critical review. Journal of Cleaner Production, Vol. 228, 801–813. DOI: 10.1016/j.jclepro.2019.04.304
Lusty, P A, Shaw, R, Gunn, A G, and Idoine, N. 2021. UK criticality assessment of technology-critical minerals and metals. British Geological Survey Commissioned Report CR/21/120N. (Nottingham, UK: British Geological Survey.)
Shaw, R A. 2021. Global lithium (Li) mines, deposits and occurrences (pdf) [online]. British Geological Survey.
Further reading
Shaw, R. 2022. The potential for lithium in the UK (pdf). British Geological Survey Commissioned Report CR/22/123. (Nottingham, UK: British Geological Survey.)
University of Birmingham. 2021. Securing technology-critical metals for Britain (pdf). (Birmingham, UK: University of Birmingham.) ISBN: 9780704429697