The UK is rapidly shifting from a fossil fuel-based economy towards cleaner energy sources. In many cases, technologies central to this transition — including wind turbines, photovoltaics and electrical vehicles — make use of a group of 17 elements collectively referred to as the rare earth elements or REEs.
The future of electric vehicles
UK sales of electric vehicles are growing rapidly, supported by a range of policy incentives including purchase grants, licensing and charge breaks and tax benefits. Their market share is anticipated to grow further in line with a UK Government commitment to end sales of new petrol and diesel vehicles by 2030.
To achieve decarbonisation in the transport sector, new value chains will need to be established and reconfigured, with implications for importing, processing and revalorisation of critical raw materials. In this section, we present information on the current and future state of embedded materials and potential demand and supply challenges for electric vehicles.
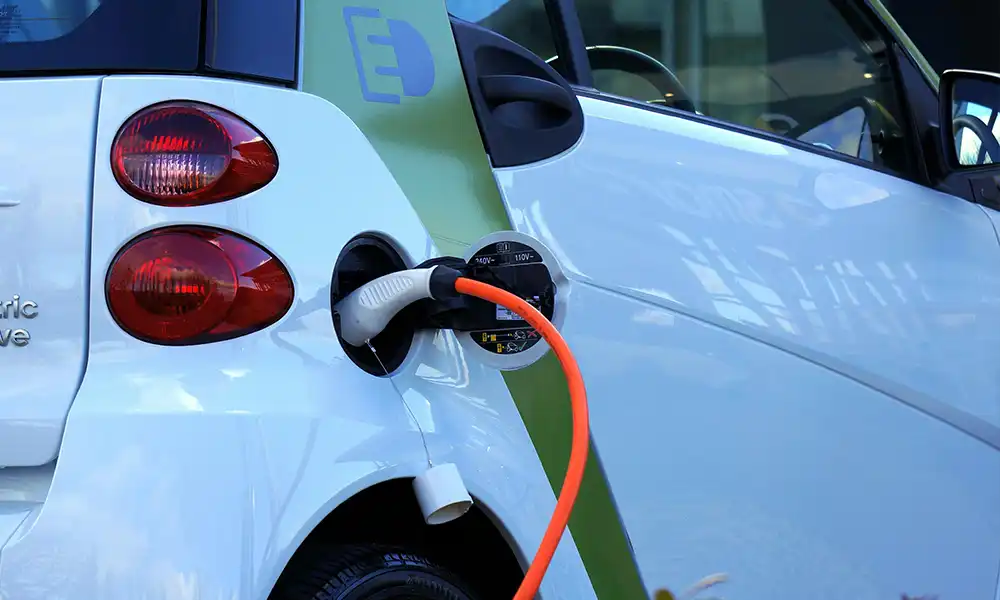
Components and metals in electric vehicles
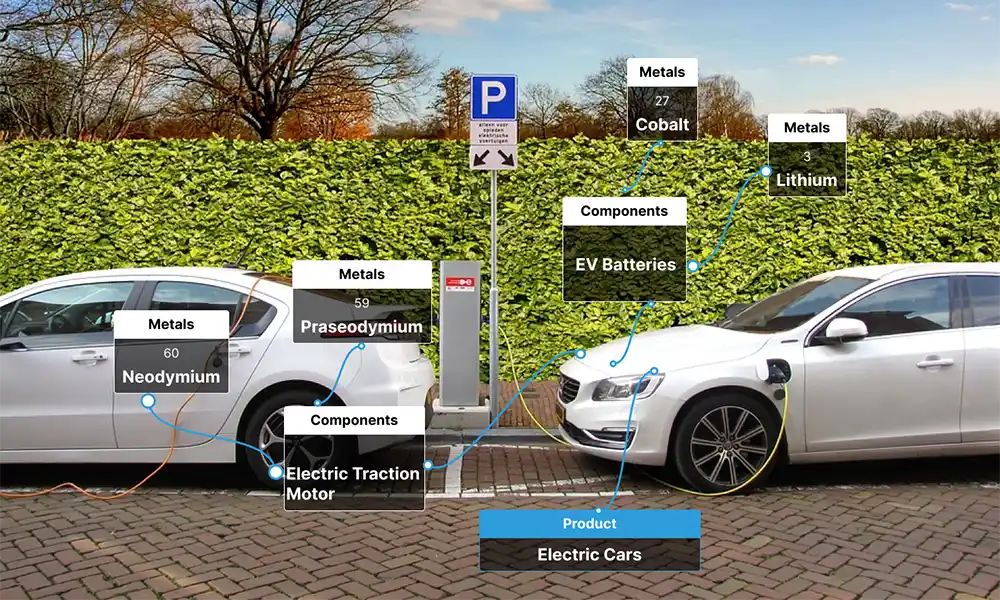
Demand
The number of licensed ultra-low emissions vehicles in the UK stood at just short of 1 million in 2022, around eight times higher than in 2017. While representing only around 2 per cent of all vehicles registered in the UK, their share of the market of new vehicles registered was far greater at roughly a fifth (Department for Transport).
This share is expected to grow and, with it, material demand for materials such as REEs, the structural, physical and chemical properties of which have cemented their place as increasingly technology-critical across a range of applications. These include in permanent magnets, catalysts and batteries (Cobelo-García et al. 2015; Zhou, 2017; Dang et al. 2021).
The UK is not alone in its aims for a low-carbon energy transition. The International Energy Agency (2020) estimates that, to meet stated policy ambitions, global demand for REEs will increase by almost four times between 2020 and 2040.
Supply
The prefix 'rare' is something of a misnomer for REEs given their relatively high abundance in the lithosphere. Low concentrations render extraction commercially unviable in many areas, however, and the UK is effectively 100 per cent import-dependent for these elements.
REE supply to the global market is concentrated in only a few countries. Of the global REE reserves, 96 percent (120 million metric tons) is concentrated in six countries (Gambogi 2021), including:
- China: 38 per cent
- Vietnam: 19 per cent
- Brazil: 18 per cent
- Russia: 10 per cent
- India: 6 per cent
- Australia: 5% per cent
China represents approximately 54 per cent of global mining supply in 2021 and is the source of approximately 95 per cent of refined supply (Roskill in Liang, 2021).
The supply chains for REEs are complex, involving the production of specialist alloys, then magnet powder, magnets themselves and finally, assembly into electric vehicles.
Prices and costs
With UK production of light-duty electric vehicles expected to increase from 0.3 to 1.5 million units from 2020 to 2030 (APC, 2021) and the UK a significant exporter of automotives (Faraday, 2021), supply constraints run the risk of negatively affecting industry output.
REEs are mined as a by-product of primarily base-metal mining (BGS, 2021), leading to a disconnect between demand and supply. Coupled with long lead times for new supply (Petravratzi and Gunn, 2022), this has led to an increase in prices.
Whilst the value of REE imports to the UK stood at just £28.5 million in 2017 (including as concentrates and compounds) these materials enter into a raft of goods produced and consumed. Diverse uses include high-value applications in catalysts, electrical equipment and magnets (BGS, 2021) as well as various product processes (Marscheider-Weidemann et al. 2021).
Disassembly
A growing stock of electric vehicles in the UK presents a potential supply opportunity in the face of high levels of demand and price increases. In the UK's Critical Minerals Strategy (BEIS, 2022), accelerating to a more circular economy with improved end-of-life treatment has been put forward as a key strategy by which to lessen security of supply risks, improve environmental performance and meet societal objectives (Bloodworth et al. 2019).
Barriers to this include:
- relatively low volumes of REEs in products
- frequently immature technologies (such as for sorting and recycling)
- supply chains to recover materials linked to high costs and exacerbated by gaps in product and component data (some data systems do exist such as the International Dismantling Information System)
Whilst permanent magnets have the potential to outlive their assembly through re-use, remanufacture and recycling, the cost of their dismantling and removal remains high and limits recycling. Data on the recovery of REEs is scant, but they are generally understood to be managed within predominantly linear value chains. Lusty et al. (2021) assume an end-of-life recycling input rate of 5.5 for REEs based on an average of light REE and heavy REE recycling rates published by the European Commission (2020).
Types, motors and technology-metal composition
The transition to electric vehicles would require access to significant quantities of technology metals, which are essential for the manufacture of electric vehicle components, such as electric powertrains and batteries. It is vital to understand different types of electric vehicles, electric traction motors and their technology metal composition, because the changing composition of electric vehicles over time creates challenges for end-of-life management and monitoring the flows and stocks.
Types of electric vehicles
- Hybrid electric vehicles (HEVs) are powered by both an electric traction motor and a combustion engine and can only be charged through regenerative braking
- Plug-in hybrid electric vehicles (PHEVs) are powered by both an electric traction motor and a combustion engine and can be charged through both regenerative braking and external power sources (a home charge point or a public charging station)
- Battery electric vehicles (BEVs) are zero-emissions vehicles powered by rechargeable batteries and electric traction motors without a petrol or diesel engine
- Hydrogen fuel cell electric vehicles (FCEVs) are a new type of electric vehicle; instead of being powered by electricity stored in a battery, FCEVs rely on the electrochemical reaction between hydrogen and oxygen in a fuel cell stack to produce electricity
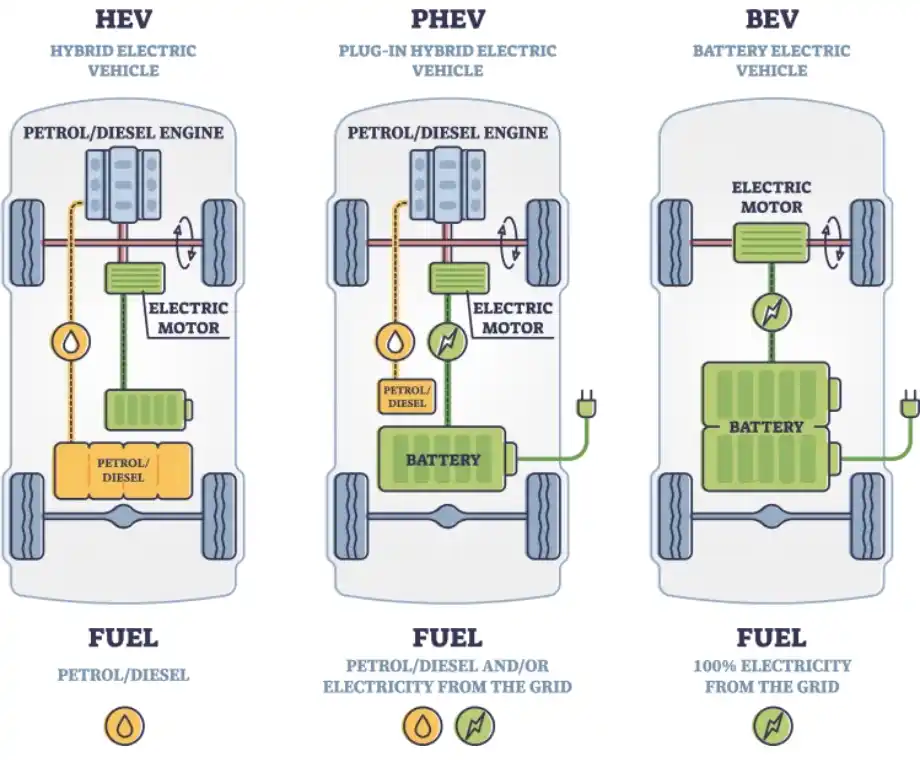
Electric traction motors
Electric traction motors used in electric vehicles can be classified into direct current motors (DC) and alternating current motors (AC) (Figure 3). The main electric traction motors are:
- Permanent magnet motors
- induction motors
- wound rotor motors
These dominate the electric vehicle market. Different model series of electric vehicles use different types of motors due to the cost of materials, power density, torque density and efficiency. Permanent magnet motors containing REEs are the most commonly used motor and their market share has been increasing in the past few years. In 2022, permanent magnet electric traction motors rose from 84 per cent in 2021 to 86 per cent of the global electric vehicle market share (IDTechEx, 2022).
Electric traction motors that contain permanent magnets include:
- brushless DC motors
- permanent magnet excited motors
- inner mounted permanent magnet motors
- surface mounted permanent magnet motors
- hybrid permanent magnet motors
- reluctance motors
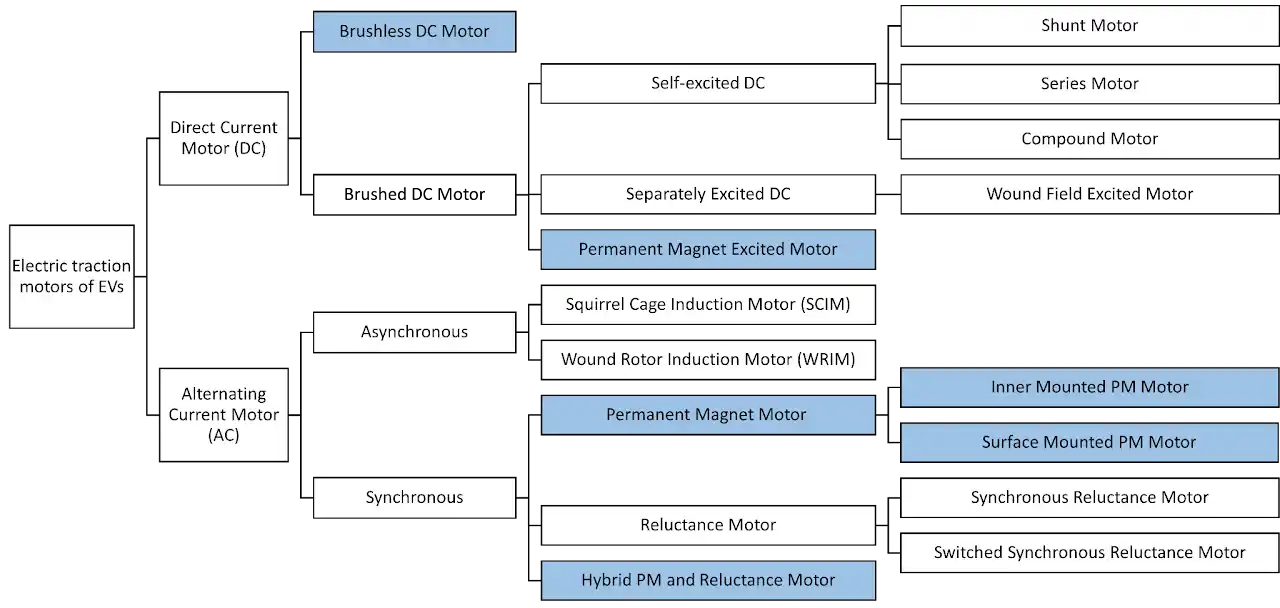
Translation into material stocks
Table 1 shows the amount of key technology metals (in terms of mass in grams) by different type of electric vehicle. The composition of the different types varies due to the different drivetrains and batteries used in the vehicles.
Metal | HEV and PHEV (Li-ion) | HEV and PHEV (NiMH) | BEV |
---|---|---|---|
Cobalt | 2712 | 8313 | 9330 |
Dysprosium | 165.72 | 165.72 | 224.63 |
Lithium | 2242 | 1.36 | 7709 |
Manganese | 5968 | 5968 | 5530 |
Neodymium | 552.79 | 2631 | 749.3 |
Nickel | 16 049 | 82 832 | 55 724 |
Praseodymium | 51.48 | 2129 | 98 |
Terbium | 13.62 | 13.62 | 29.93 |
Legal and regulatory considerations
As a result of policy shift to electric mobility, the number of electric vehicles in use is leading to greater volume of electric vehicle lithium-ion batteries with associated issues around capacity, transport, safety and waste shipment regulations. Policy and regulatory interventions are required in order to address this challenge.
- Developing clear regulation and policy on re-use and repurposing, including the influencing of contractual and ownership models (for example, battery leasing schemes) for electric vehicle batteries to facilitate recycling and second use. This intervention will help to develop appropriate business models that will promote re-use and safe and effective life-management of electric vehicle batteries. An important precondition is developing clear, legal definitions of what 're-use', 'repurposing' and 'recycling' entail, which should be done within the wider aim of revisiting the definition of 'waste' under the Waste Framework Directive
- Developing extended producer responsibility regulations that support a move to a circular economy model, ensuring safe and effective re-use of electric vehicle batteries, with increasingly robust recycling targets. This regulatory intervention will assist in increasing the recycling and recovery of material within electric vehicle batteries
- Developing eco-design criteria for recycling and remanufacturing, including restrictions on the use of hazardous substances and promotion of designs that allow easy separation of parts, which will facilitate dismantling and component separation and lead to greater economic viability of recycling
- Introducing mandatory chemistry labelling requirements for lithium-ion batteries to enable end-of-life lithium batteries to be easily and safely sorted and separated for recycling in specific groups. Currently, there is no legal requirement to label the cathode chemistry on a battery pack (which is coupled with a variety of different technologies on the market). This measure will facilitate separation of batteries at the end of their lives and recycling of batteries containing same or similar properties
- More information on legal and regulatory considerations
More information
References
Ortego, A, Valero, A, Valero, A, and Restrepo, E. 2018. Vehicles and critical raw materials: a sustainability assessment using thermodynamic rarity. Journal of Industrial Ecology, Vol. 22(5), 1005–10151. DOI: 10.1111/jiec.12737
Further reading
Iglesias-Émbil, M, Valero, A, Ortego, A, Villacampa, M, Vilaró, J, and Villalba, G. 2020. Raw material use in a battery electric car-a thermodynamic rarity assessment. Resources, Conservation and Recycling, Vol. 158, 104820. DOI: 10.1016/j.resconrec.2020.104820