Lithium-ion batteries will enable the transition from hydrocarbon fuels as a dense store of energy in vehicles to vehicles with no carbon emissions at the point of use. Their production is imperative to enable the decarbonisation of the transport sector. Although transportation will be one of the major consumers of lithium-ion batteries, there will also be applications in a wide range of other sectors.
There are a range of different lithium-ion battery chemistries (Figure 1), each of which have different performance criteria that make them suited for different applications. All lithium-ion batteries contain lithium, but some of the different chemistries that offer higher performance (extended range and power) are more reliant on certain technology-critical metals like cobalt and nickel.
Given how important batteries and the technology-critical metals they contain are to our economy, it is essential to ensure the good custody of these materials and ensure that they return to the economy at the end of the batteries' lives.
Disassembly
When designing battery packs for the full life cycle, ensuring easy disassembly will enable a range of options including repair, remanufacture, re-use and recycling when the packs reach the end of their lives. If batteries can be disassembled, the technology metals they contain can be kept in higher-value states and recycled more effectively.
Currently, many of the processes for recycling batteries involve putting them into a shredder. This reduces the variety of battery packs to a uniform product that can be easily handled. Unfortunately, mixing the material streams of technology metals with other contaminants means that recycling processes become more complex and less profitable, often resulting in material downcycling.
Recycling
The key to efficient battery recycling comes in retaining high-purity cathode active material (CAM). There are several sources of battery material, including end-of-life vehicles, production scrap and insurance returns.
CAMs can be dealt with in different ways and most currently start with shredding under an inert atmosphere or under vacuum. This is usually followed by physical techniques, including magnetic, electrostatic and eddy-current separation. These tend to be followed by acidic or basic digestion of the CAM, followed by precipitation and calcination. This may involve more than 10 steps, some of which may use high-temperature methods.
Met4Tech has been developing new flowsheets for processing CAMs using robotic separation and ultrasonic delamination to speed up material processing and yield purer material, particularly from production scrap. Some of the key challenges include cell opening, binder separation and low-temperature regeneration.
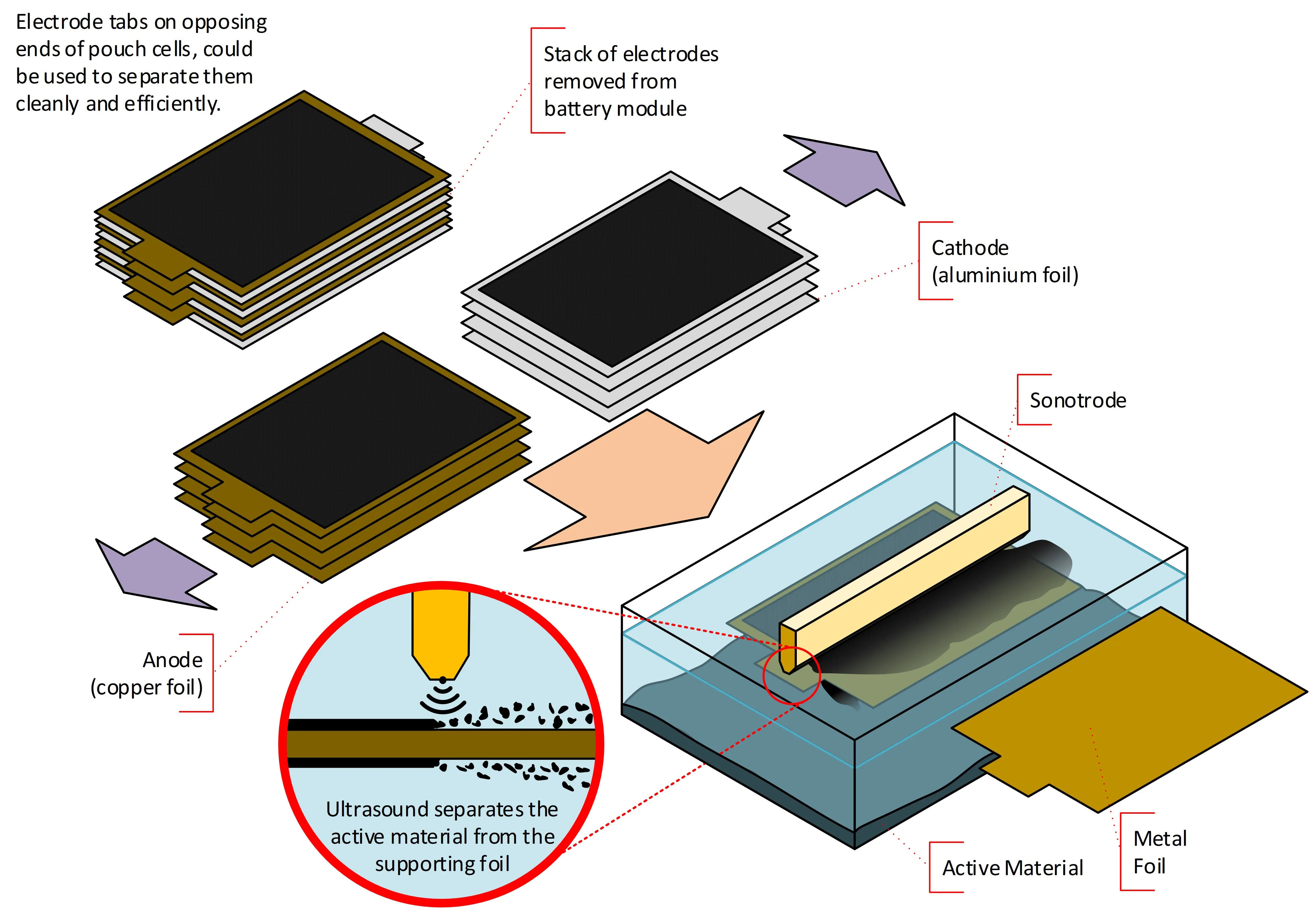
Legal and regulatory considerations
As a result of policy shift to electric mobility, the number of electric vehicles in use is leading to a greater volume of lithium-ion batteries coupled with issues around capacity, transport, safety and waste-shipment regulations. To address this challenge, a set of policy and regulatory interventions is required.
Re-use and repurposing
Clear regulation and policy on re-use and repurposing need to be developed, including the influencing of contractual and ownership models (for example, battery leasing schemes) for electric vehicle batteries, to facilitate recycling and second use. This will help to develop appropriate business models that will promote re-use and safe and effective life management of electric vehicle batteries.
An important precondition is developing clear, legal definitions of what 're-use', 'repurposing' and 'recycling' entail, which should be done with the wider aim of revisiting the definition of 'waste' under the Waste Framework Directive.
Producer responsibility regulations
Extended producer responsibility regulations are needed to support a move to a circular economy model, ensuring safe and effective re-use of electric vehicle batteries with increasingly robust recycling targets. This regulatory intervention will assist in increasing the recycling and recovery of material within electric vehicle batteries.
Eco-design criteria
Design criteria for recycling and re-manufacturing should include restrictions on the use of hazardous substances and promotion of designs that allow easy separation of parts. This regulatory intervention will facilitate dismantling and component separation, leading to a greater economic viability of recycling. A crucial aspect of battery cell design is the use of non-fluorinated binders in the cell, which, together with joining methods between cells and modules, will enable automated disassembly.
Labelling requirements
Currently, there is no legal requirement to label the cathode chemistry on a battery pack that is coupled with a variety of different technologies on the market. The introduction of mandatory chemistry labelling requirements for lithium-ion batteries will enable easy and safe sorting and separating for recycling of end-of-life batteries in specific groups. This measure will facilitate separation of batteries at the end of their lives and recycling of batteries with the same or similar components.
More information
References
The Faraday Institution. 2021. Faster, greener technique invented to improve recycling process for electric vehicle batteries. The Faraday Institution.