In a circular economy, recycling is a preferred option after re-use, repair, remanufacture and refurbishment. In recycling, an obsolete product is processed to recover and produce new materials, such as technology metals.
Recycling offers both environmental and energy benefits. For example, if electronic waste (e-waste) is put into a landfill site, heavy metals and hazardous chemicals could be released, which may have a negative effect on human health and the environment.
Compared to mining, metal recycling uses less energy and saves resources. To produce one tonne of lithium carbonate, 300 tonnes of rock must be processed and around 370 tonnes of brine. Recycling 28 tonnes of lithium-ion batteries from electric vehicles can produce the same amount of lithium.
However, recycling suffers from insufficient collection. In the case of technology metals, their recycling rates are very low. This is due to their being used in small amounts in a myriad of products and often in complex configurations. Recycling of technology metals therefore requires new and innovative technologies. 'Design for recycling' is of fundamental importance to ensure that the efficiency of recycling increases, as do improvements in collection and segregation processes.
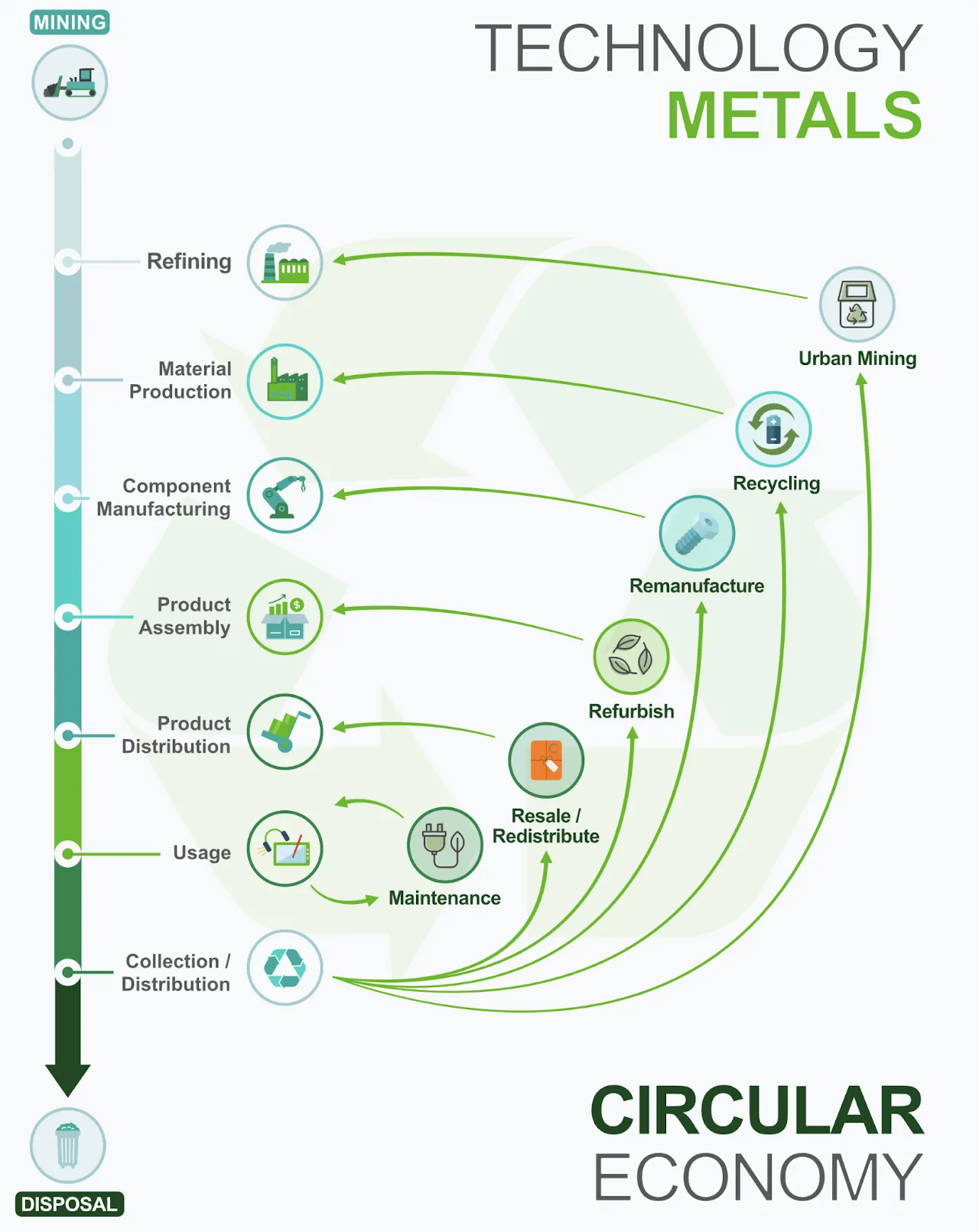
Recycling metals
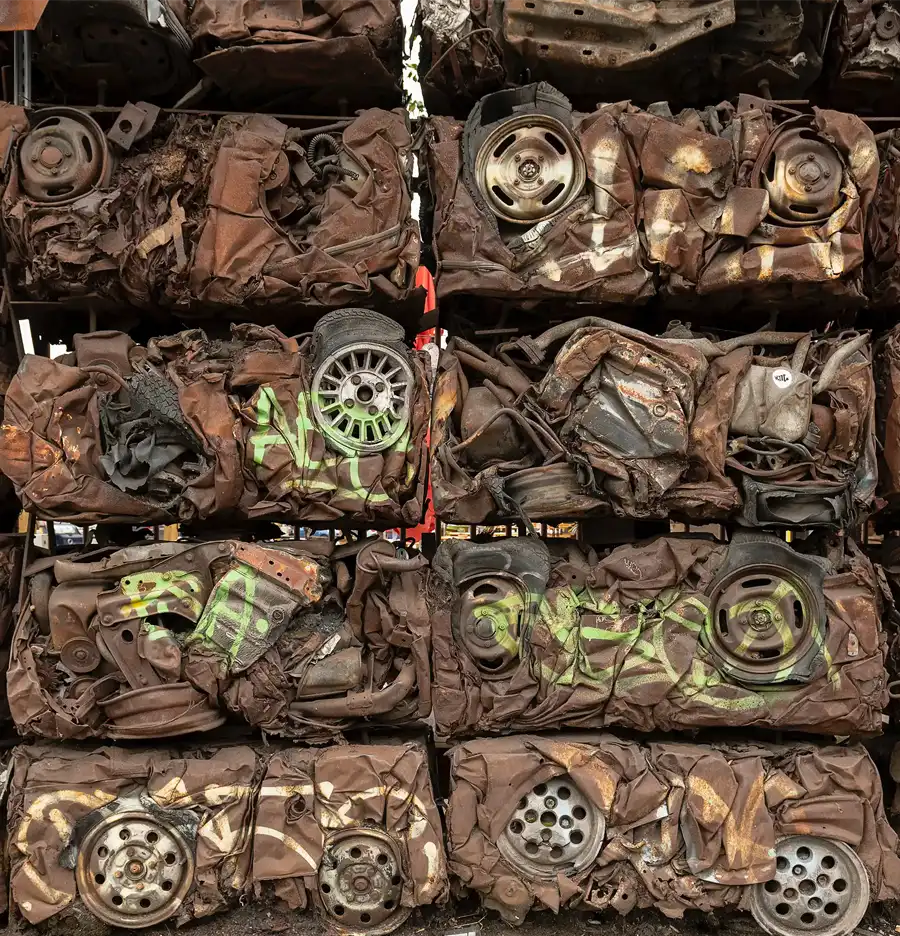
Recycling enables the recovery of metals that are essential for the decarbonisation of the economy, such as copper, lithium and nickel. These metals are found in various quantities in everyday objects including:
- electrical and electronic waste
- vehicles
- packaging
They are also found in industrial equipment and processes that derive metal waste.
Recycling rates may vary substantially depending on the end-of-life product or waste stream characteristics. For example, e-waste recycling involves dealing with complex waste composed of three different layers: metals, organic materials (plastics, etc.) and inorganic materials (ceramics; glass).
Recycling processes
Current recycling processes involve:
- physical methods: shredding the materials to reduce their size frees the metals from any casing. Inorganic materials, metals and organic materials are then separated according to their different physical properties (magnetism; density; electrical conductivity, etc.). However, a fraction of the metals is lost during the process and hazardous dusts are likely to be produced
- pyrometallurgical processes: subjecting the waste to very high temperatures allows the metals to be concentrated in an ingot. Organic materials are used as fuel for the process, but their incineration releases hazardous gases and chemicals. Inorganic materials produce slag in which some metals are lost
- hydrometallurgical processes: these use strong chemicals (acids; bases; oxidants) to dissolve metals in aqueous solutions. This method consumes large quantities of chemicals and produces hazardous liquid wastes. The limitations of current processes must be addressed by developing innovative and sustainable processes for metal recovery.
Very often, recycling processes use a combination of physical, pyrometallurgical and hydrometallurgical methods to recover high-purity metals.
A new era for metal recycling
Until now, metal recycling has focused on IT equipment and e-waste (smartphones; refrigerators; televisions, etc.), which contain small amounts of technology metals. The collection of this type of waste is difficult because the items are scattered among different households.
In the near future, new sources of waste will appear and make recycling more favourable. These items will contain large quantities of metals (lithium-ion batteries from electric vehicles; magnets from wind turbines, etc.). They will be easier to collect because large quantities are in one place (solar and wind farms) and their life span is predictable. The value of the metals contained is also higher, giving rise to greater economic incentives for recycling (platinum group metals in catalysts for hydrogen production, etc).
Better processes
Innovative methods are emerging to improve metal recycling. These methods would improve the collection of dispersed technology waste through the use of digital product passports. They would improve the sorting and separation of different wastes through the use of artificial intelligence ('computer vision').
Current processes involve shredding, burning or dissolving inorganic, organic and metallic phases without distinction. A better approach to recycling is the use of tools specifically designed to target weaknesses at the interface between these different layers. Such tools include:
- ultrasound, which can selectively remove brittle inorganic layers
- chemical approaches to selectively dissolve organic layers
- selective dissolution of metals using sustainable solvents
- hydrogen embrittlement for the recovery of lanthanide elements in magnets
Legal and regulatory considerations
- Recycling targets vary for different products and generally do not focus on component materials. Currently, recycling targets for products rich in critical minerals, such as electric vehicle batteries, are somewhat crudely defined in terms of setting a target by overall weight of product. For example, for electric vehicles, the overall target is only 85 to 95 per cent by weight: this target does not necessarily help recover the most valuable material. More targeted legislation is needed to recover materials of greatest value.
- Widespread re-use will have negative effects on the recycling industry
- Transportation of hazardous materials for recycling involves costs and safety risks
- Extended producer responsibilities only apply to specific product streams, for example waste electrical and electronic equipment; vehicles; batteries
- We need to design for recycling to ensure ease of dismantling and disassembly, both of which can facilitate recycling
- Incentives and better awareness for consumers are needed
- There needs to be policy incentives for recycling and permitting mechanisms to facilitate recycling, such as metal recovery conditions targeted to critical metals
- Smarter collection mechanisms reduce cost and effort for consumer to recycle, such as portable batteries